一 : 2003年质量工程师资格考试考题精选一
1. 加工零件需三道工序,每道工序不合格品率为2%,3%,7%,求该件的不合格品率?
11、知r1 是(x1,y1),r2(x1+a,y1+a)问线关系数
a,r1r2 c,r1=r2
r1=lxy/√(lxxlyy)
=∑(xi-e(x))(yi-e(y))/√(∑(xi-e(x))^2×∑(yi- e(y)) ^2)
e(x+a)=e(x)+a
r2= lxiyi/√(lxixilyiyi)
=∑((xi+a)-e(x+a))((yi+b)-e(y+b))/√(∑(xi+a-e(x+a))^2×∑(yi+b-e(y+b))^2)
=∑((xi+a)-(e(x)+a))((yi+b)-(e(y)+b))/√(∑(xi+a-(e(x)+a))^2×∑(yi+b-(e(y)+b))^2)
=∑((xi-e(x))(yi-e(y))/√(∑(xi-e(x))^2×∑(yi-e(y))^2)
r1=r2
3.属于周期性检验的是
a,连续型的全部产品 b,连续型中的第一批产品,
c,新产品 d,连续型中的新产品
14,标准型抽样中p1/p0,这个比值越小则
a,越高 b,越差 b,没有影响 d,不能确定
31、质量改进和质量控制都是质量管理的一部分,其差别在于:
a、一个强调持续改进,一个没有强调
b、一个为了提高质量,一个为了稳定质量
c、一个是全员参与,一个是部分人参与
d、一个要用控制图,一个不需要
32、朱兰质量管理三部曲:
a: 质量策划、质量控制、质量改进 b:质量策划、质量控制、质量保证
c:质量策划、质量控制、质量检验 d: 质量策划、质量检验、质量保证
33、人机料法环五个因素中,考虑检验人员是否会正确使用测量仪器,属于()
a,人 b,机 c,法 d环
34、设立假说是分析问题原因时必经的一个过程,()可以用来帮助建立假说:
a 矩阵图 b pdpc法 c 因果图 d排列图
35、质量改进过程中“明确问题”阶段用的统计工具有:
a 因果图 b 直方图 c pdoc法 d系统图
36、某公司生产的新型电路板其有100个焊点,这些焊点不能出现虚焊或连焊等缺陷。在过去一个月中共生产了10000块这样的电路板,发现虚焊连焊等缺陷6000个,这个生产过程的dpmo为
a 0.6 b 60 c 600 d 6000
37、已知x服从指数分布p(x=0在入=0.1的情况p(5r2 b,r2>r1 c,r1=r2 d,以上均不对.
四、控制图的tl=46。5,tu=54。5,x(上面二杠)=50。5,s(上面一杠)=2。52,a2=2。12,a3=1。47,d4=3。45,d3=0,b4=0。96,b3=0,则:
1、x图的上下控制线是多少?
2、s的上下控制线是多少?
3、过程能力是多少 ?
4、cpk是多少?
5、54。3、53。1、52。2是否在控制线内?
1设x1,x2,x3.......xn服从(0,1)的均匀分布,令y=x1+x2+x3......xn-6;问y的均值和标准差为
a,e(y)=0 b,var(y)=1/12 c,e(y)=6 d,var(y)=0
*有一个产品可靠性试验,到定时截尾时间为t,出现的故障数为y,以下说法正确的是:答案见p208页
*关于抽样方案(n,n,a),则下列说法正确的是( )
a、n,n为定值时,a增大,oc曲线由下向上移动
b、n,n为定值时,a增大,oc曲线由上向下移动
c、n,a为定值时,n增大,oc曲线由下向上移动
d、n,a为定值时,n增大,oc曲线由上向下移动
5。4。1与5。4。2
4、已知随机变量x服从二页分布,且e(x)=2。4 ,d(x)=1。44,则二项分布的参数n,p为( )
a、n=4,p=0。6 b、n=6 p=0。4 c:? d、?
好象有这样的两道题(靠回忆,忘了题号):
下列变量之间属于相关关系的有:
1)父亲的身高和儿子的身高 2)人的身高和体重
3)圆的面积和半径 4)电路中的电流和电压
常用的可靠性分析方法有:
1)fmeca 2)pdpc 3)fta 4)pdca 5)fracas
有一题关于控制图两类错误的。
有一题 求偏方和
a,max(t1,t2...tn)--m(t1,t2,...tn)
b,s=xigm上面是4下面是i(ti-y)平方
c------
d-----
还有一题:
关于oc曲线的。
具体内容不记得了,是oc曲线p0点是生产方风险质量,批拒收概率为a,p1点为使用方风险质量,批接受概率为b。
有一题比较简单
规定的时间指
a,一天
b,一年
c,安培
d,次数
e,里程
这题好像是送分的
有一题是序贯抽样的(一个一个抽判一批合格?)
还有一题是关于可靠性测定试验方面的?
选:t/r,2r/[(2r+r)*..]
二 : 质量师考试心得
第一点:对教材的全面掌握是不能放松的
考生往往希望复习的范围越小越好,甚至有部分考生把全部希望寄托在辅导老师考前的押题上,这种心情可以理解,但实践证明,要想顺利通过质量资格考试,对教材的全面掌握是不能放松的。考试试题基本上是不会超出教材范围的,考试教材包含了命题范围和答案标准,你必须按指定教材的内容、观点和要求去回答考试中的所有问题,否则你很难获得高分。所以教材是考试的根本。考生千万不可抱有侥幸心理,只有充分准备,在考试时才能游刃有余。
有了教材,还必须善于总结与系统把握教材的精髓。善于总结就是在仔细看完一篇教材的前提下,一边看书,一边作总结性的笔记,把教材中每一章的要点都列出来,而且要系统地把握考试课程之间的密切联系。强调对教材的掌握,是要突出全面理解,并不是要求考生把指定教材的全部内容逐字逐句地背下来。掌握教材需要一定的时间和精力投入,考生宜早做安排。
第二点:把握各科目知识点的重点
除了掌握教材,考生也要注意抓住重点进行复习。因为质量资格考试两门科目知识点的重要性是不一样的。每门课程都有其必考知识点,这些知识点在每年的试卷上都会出现,只是形式不同。对于重要的知识点,考生一定要深刻把握,能够举一反三。考生在复习中要想提高效率,就必须把握重点,这样才能能使考生以较小的投入获取较大的考试收益。
第三点:多做一些高质量的练习题和模拟题
质量资格考试涉及内容十分广泛,有些内容实际业务中很少接触,仅仅依靠记忆和自身理解来准备考试是远远不够的。从某种意义上讲,考试就是做题。所以在学习的过程中多做一些高质量的练习题和模拟题,使考生尽快熟悉考试题型并提高对相关知识点的理解,进而提高应试能力。
三 : 监理工程师工程质量控考试辅导第七章
第一节 质量统计基本知识 一、总体、样本及统计推断工作过程
1 .总体
总体也称母体,是所研究对象的全体。个体,是组成总体的基本元素。总体中含有个体的数目通常用n表示。在对一批产质量检验时,该批产品是总体,其中的每件产品是个体,这时n是有限的数值,则称之为有限总体。若对生产过程进行检测时,应该把整个生产过程过去、现在以及将来的产品视为总体。随着生产的进行n是无限的,称之为无限总体。实践中一般把从每件产品检测得到的某一质量数据(强度、几何尺寸、重量等)即质量特性值视为个体,产品的全部质量数据的集合即为总体。
2 .样本
样本也称子样,是从总体中随机抽取出来,并根据对其研究结果推断总体质量特征的那部分个体。被抽中的个体称为样品,样品的数目称样本容量,用n表示。
3 .统计推断工作过程
质量统计推断工作是运用质量统计方法在生产过程中或一批产品中,随机抽取样本,通过对样品进行检测和整理加工,从中获得样本质量数据信息,并以此为依据,以概率数理统计为理论基础,对总体的质量状况作出分析和判断。质量统计推断工作过程见教材134页图7-1。
二、质量数据的收集方法
( 一 ) 全数检验
全数检验是对总体中的全部个体逐一观察、测量、计数、登记,从而获得对总体质量水平评价结论的方法。
( 二 ) 随机抽样检验 抽样检验是按照随机抽样的原则,从总体中抽取部分个体组成样本,根据对样品进行检测的结果,推断总体质量水平的方法。
抽样检验抽取样品不受检验人员主观意愿的支配,每一个体被抽中的概率都相同,从而保证了样本在总体中的分布比较均匀,有充分的代表性;同时它还具有节省人力、物力、财力、时间和准确性高的优点;它又可用于破坏性检验和生产过程的质量监控,完成全数检测无法进行的检测项目,具有广泛的应用空间。抽样的具体方法有:
1 .简单随机抽样 简单随机抽样又称纯随机抽样、完全随机抽样,是对总体不进行任何加工,直接进行随机抽样,获取样本的方法。
2 .分层抽样 分层抽样又称分类或分组抽样,是将总体按与研究目的有关的某一特性分为若干组,然后在每组内随机抽取样品组成样本的方法。
3 .等距抽样 等距抽样又称机械抽样、系统抽样,是将个体按某一特性排队编号后均分为n组,这时每组有 k二n/n个个体,然后在第一组内随机抽取第一件样品,以后每隔一定距离(k号)抽选出其余样品组成样本的方法。如在流水作业线上每生产100件产品抽出一件产品做样品,直到抽出n件产品组成样本。
4 .整群抽样 整群抽样一般是将总体按自然存在的状态分为若干群,并从中抽取样品群组成样本,然后在中选群内进行全数检验的方法。如对原材料质量进行检测,可按原包装的箱、盒为群随机抽取,对中选箱、盒做全数检验;每隔一定时间抽出一批产品进行全数检验等。
由于随机性表现在群间,样品集中,分布不均匀,代表性差,产生的抽样误差也大,同时在有周期性变动时,也应注意避免系统偏差。
5 .多阶段抽样 多阶段抽样又称多级抽样。上述抽样方法的共同特点是整个过程中只有一次随机抽样,因而统称为单阶段抽样。但是当总体很大时,很难一次抽样完成预定的目标。多阶段抽样是将各种单阶段抽样方法结合使用,通过多次随机抽样来实现的抽样方法。如检验钢材、水泥等质量时,可以对总体按不同批次分为r群,从中随机抽取r群,而后在中选的r群中的m个个体中随机抽取m个个体,这就是整群抽样与分层抽样相结合的二阶段抽样,它的随机性表现在群间和群内有两次。
[ 例题 ]: 对总体中的全部个体逐一观察、测量、计数、登记,从而获得对总体质量水平评价结论的方法是( )。
a. 全数检验 b. 随机抽样检验 c. 简单随机抽样 d. 分层抽样
答案:a
三、质量数据的分类
质量数据是指由个体产品质量特性值组成的样本(总体)的质量数据集,在统计上称为变量;个体产品质量特性值称变量值。根据质量数据的特点,可以将其分为计量值数据和计数值数据。
1 .计量值数据
计量值数据是可以连续取值的数据,属于连续型变量。其特点是在任意两个数值之间都可以取精度较高一级的数值。它通常由测量得到,如重量、强度、几何尺寸、标高、位移等。此外,一些属于定性的质量特性,可由专家主观评分、划分等级而使之数量化,得到的数据也属于计量值数据。
2 .计数值数据
计数值数据是只能按0,1,2,……数列取值计数的数据,属于离散型变量。它一般由计数得到。计数值数据又可分为计件值数据和计点值数据。
(1)计件值数据,表示具有某一质量标准的产品个数。如总体中合格品数、一级品数。
(2)计点值数据,表示个体(单件产品、单位长度、单位面积、单位体积等)上的缺陷数、质量问题点数等。如检验钢结构构件涂料涂装质量时,构件表面的焊渣、焊疤、油污、毛刺数量等。
[ 例题 ]:根据质量数据的特点,可以将其分为( )。
a. 计量值数据 b. 计数值数据 c. 计件值数据 d. 计点值数据 e.计价值数据
答案:ab
四、质量数据的特征值
样本数据特征值是由样本数据计算的描述样本质量数据波动规律的指标。统计推断就是根据这些样本数据特征值来分析、判断总体的质量状况。常用的有描述数据分布集中趋势的算术平均数、中位数和描述数据分布离中趋势的极差、标准偏差、变异系数等。
( 一 ) 描述数据集中趋势的特征值
1 .算术平均数
算术平均数又称均值,是消除了个体之间个别偶然的差异,显示出所有个体共性和数据一般水平的统计指标,它由所有数据计算得到,是数据的分布中心,对数据的代表性好。其计算公式为:
(1) 总体算术平均数υ
υ=1/n(x1+x2+…+xn)=1/nσxi
式中 n——总体中个体数;
xi——总体中第i个的个体质量特性值。
(2)样本算术平均数
2. 样本中位数。
样本中位数是将样本数据按数值大小有序排列后,位置居中的数值。当样本数n为奇数时,数列居中的一位数即为中位数;当样本数n为偶数时,取居中两个数的平均值作为中位数。(二) 描述数据离中趋势的特征值
1. 极差 r
极差是数据中最大值与最小值之差,是用数据变动的幅度来反映其分散状况的特征值。极差计算简单、使用方便,但粗略,数值仅受两个极端值的影响,损失的质量信息多,不能反映中间数据的分布和波动规律,仅适用于小样本。其计算公式为:
r=xmax—xmin
2.标准偏差。
标准偏差简称标准差或均方差,是个体数据与均值离差平方和的算术平均数的算术根,是大于0的正数。总体的标准差用σ表示;样本的标准差用s表示。标准差值小说明分布集中程度高,离散程度小,均值对总体(样本)的代表性好;标准差的平方是方差,有鲜明的数理统计特征,能确切说明数据分布的离散程度和波动规律,是最常用的反映数据变异程度的特征值。
(1)总体的标准偏差σ(2)样本的标准偏差s
样本的标准偏差s是总体标准差σ的无偏估计。
(3)变异系数cv
变异系数又称离散系数,是用标准差除以算术平均数得到的相对数。它表示数据的相对离散波动程度。变异系数小,说明分布集中程度高,离散程度小,均值对总体(样本)的代表性好。由于消除了数据平均水平不同的影响,变异系数适用于均值有较大差异的总体之间离散程度的比较,应用更为广泛。其计算公式为:
cv=σ/μ(总体)
[ 例题 ]:( )是数据中最大值与最小值之差,是用数据变动的幅度来反映其分散状况的特征值。
a. 极差 b. 标准偏差 c. 变异系数 d. 算术平均数
答案:a
五、质量数据的分布特征
( 一 ) 质量数据的特性
质量数据具有个体数值的波动性和总体(样本)分布的规律性。
在实际质量检测中,我们发现即使在生产过程是稳定正常的情况下,同一总体(样本)的个体产品的质量特性值也是互不相同的。这种个体间表现形式上的差异性,反映在质量数据上即为个体数值的波动性、随机性,然而当运用统计方法对这些大量丰富的个体质量数值进行加工、整理和分析后,我们又会发现这些产品质量特性值(以计量值数据为例)大多都分布在数值变动范围的中部区域,即有向分布中心靠拢的倾向,表现为数值的集中趋势;还有一部分质量特性值在中心的两侧分布,随着逐渐远离中心,数值的个数变少,表现为数值的离中趋势。质量数据的集中趋势和离中趋势反映了总体(样本)质量变化的内在规律性。
(二)质量数据波动的原因
众所周知,影响产品质量主要有五方面因素,即人,包括质量意识、技术水平、精神状态等;材料,包括材质均匀度、理化性能等;机械设备,包括其先进性、精度、维护保养状况等;方法,包括生产工艺、操作方法等;环境,包括时间、季节、现场温湿度、噪声干扰等;同时这些因素自身也在不断变化中。个体产品质量的表现形式的千差万别就是这些因素综合作用的结果,质量数据也因此具有了波动性。
质量特性值的变化在质量标准允许范围内波动称之为正常波动,是由偶然性原因引起的;若是超越了质量标准允许范围的波动则称之为异常波动,是由系统性原因引起的。
[ 例题 ] :质量特性值的变化在质量标准允许范围内波动称之为正常波动,是由( )原因引起的。
a. 系统性 b.偶然性 c. 特殊 d.一般
答案:b
1 .偶然性原因
在实际生产中,影响因素的微小变化具有随机发生的特点,是不可避免、难以测量和控制的,或者是在经济上不值得消除,它们大量存在但对质量的影响很小,属于允许偏差、允许位移范畴,引起的是正常波动,一般不会因此造成废品,生产过程正常稳定。通常把4m1e因素的这类微小变化归为影响质量的偶然性原因、不可避免原因或正常原因。
2 .系统性原因
当影响质量的4m1e因素发生了较大变化,如工人未遵守操作规程、机械设备发生故障或过度磨损、原材料质量规格有显著差异等情况发生时,没有及时排除,生产过程则不正常,产品质量数据就会离散过大或与质量标准有较大偏离,表现为异常波动,次品、废品产生。这就是产生质量问题的系统性原因或异常原因。由于异常波动特征明显,容易识别和避免,特别是对质量的负面影响不可忽视,生产中应该随时监控,及时识别和处理。
( 三 ) 质量数据分布的规律性
对于每件产品来说,在产品质量形成的过程中,单个影响因素对其影响的程度和方向是不同的,也是在不断改变的。众多因素交织在一起,共同起作用的结果,使各因素引起的差异大多互相抵消,最终表现出来的误差具有随机性。对于在正常生产条件下的大量产品,误差接近零的产品数目要多些,具有较大正负误差的产品要相对少,偏离很大的产品就更少了,同时正负误差绝对值相等的产品数目非常接近。于是就形成了一个能反映质量数据规律性的分布,即以质量标准为中心的质量数据分布,它可用一个“中间高、两端低、左右对称”的几何图形表示,即一般服从正态分布。
概率数理统计在对大量统计数据研究中,归纳总结出许多分布类型,如一般计量值数据服从正态分布,计件值数据服从二项分布,计点值数据服从泊松分布等。实践中只要是受许多起微小作用的因素影响的质量数据,都可认为是近似服从正态分布的,如构件的几何尺寸、混凝土强度等;如果是随机抽取的样本,无论它来自的总体是何种分布,在样本容量较大时,其样本均值也将服从或近似服从正态分布。因而,正态分布最重要、最常见、应用最广泛。正态分布概率密度曲线如下图所示。
第二节 调查表法、分层法、排列图法与因果图法 一、统计调查表法 统计调查表法又称统计调查分析法,它是利用专门设计的统计表对质量数据进行收集、整理和粗略分析质量状态的一种方法。
在质量控制活动中,利用统计调查表收集数据,简便灵活,便于整理,实用有效。它没有固定格式,可根据需要和具体情况,设计出不同统计调查表。常用的有:
(1)分项工程作业质量分布调查表;
(2)不合格项目调查表;
(3)不合格原因调查表;
(4)施工质量检查评定用调查表等。
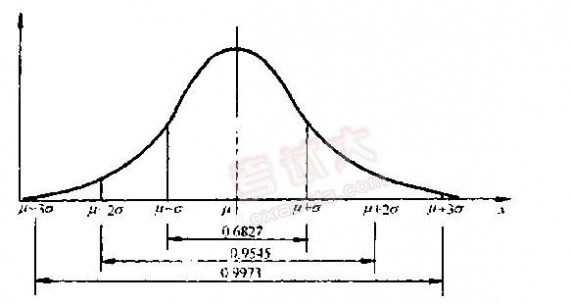
混凝土空心板外观质量问题调查表 表7-1
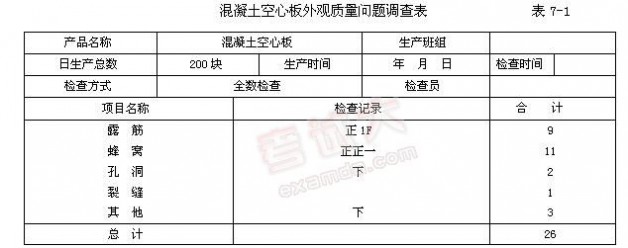
应当指出,统计调查表往往同分层法结合起来应用,可以更好、更快地找出问题的原因,以便采取改进的措施。
二、分层法
分层法又叫分类法,是将调查收集的原始数据,根据不同的目的和要求,按某一性质进行分组、整理的分析方法。分层的结果使数据各层间的差异突出地显示出来,层内的数据差异减少了。在此基础上再进行层间、层内的比较分析,可以更深入地发现和认识质量问题的原因。由于产品质量是多方面因素共同作用的结果,因而对同一批数据,可以按不同性质分层,使我们能从不同角度来考虑、分析产品存在的质量问题和影响因素。
常用的分层标志有:
(1)按操作班组或操作者分层;
(2)按使用机械设备型号分层;
(3)按操作方法分层;
(4)按原材料供应单位、供应时间或等级分层;
(5)按施工时间分层;
(6)按检查手段、工作环境等分层。
[ 例 7-1]:钢筋焊接质量的调查分析,共检查了50个焊接点,其中不合格19个,不合格率为38%。存在严重的质量问题,试用分层法分析质量问题的原因。现已查明这批钢筋的焊接是由a、b、c三个师傅操作的,而焊条是由甲、乙两个厂家提供的。因此,分别按操作者和焊条生产厂家进行分层分析,即考虑一种因素单独的影响,见表7-2和表7-3。
由表7—2和表7—3分层分析可见,操作者b的质量较好,不合格率25%;而不论是采用家厂还是乙厂的焊条,不合格率都很高且相差不大。为了找出问题之所在,再进一步采用综合分层进行分析,即考虑两种因素共同影响的结果,见表7-4。
分层法是质量控制统计分析方法中最基本的一种方法。其他统计方法一般都要与分层法配合使用,如排列图法、直方图法、控制图法、相关图法等,常常是首先利用分层法将原始数据分门别类,然后再进行统计分析的。
[
例题 ] :( )是质量控制统计分析方法中最基本的一种方法。其他统计方法一般都要与之配合使用。
a. 排列图法 b. 分层法 c. 直方图法 d. 相关图法
答案:b
三、排列图法
1 .排列图法的概念
排列图法是利用排列图寻找影响质量主次因素的一种有效方法。排列图又叫帕累托图或主次因素分析图,它是由两个纵坐标、一个横坐标、几个连起来的直方形和一条曲线所组成。实际应用中,通常按累计频率划分为(0%—80%)、 (80%—90%)、 (90%-100%)三部分,与其对应的影响因素分别为a、b、c三类。a类为主要因素,b类为次要因素,c类为一般因素。
2 .排列图的作法
下面结合实例加以说明。
[ 例 7—2]: 某工地现浇混凝土构件尺寸质量检查结果是:在全部检查的8个项目中不合格点(超偏差限值)有150个,为改进并保证质量,应对这些不合格点进行分析,以便找出混凝土构件尺寸质量的薄弱环节。
(1)收集整理数据
首先收集混凝土构件尺寸各项目不合格点的数据资料,见教材141页表7—5。各项目不合格点出现的次数即频数。然后对数据资料进行整理,将不合格点较少的轴线位置、预埋设施中心位置、预留孔洞中心位置三项合并为“其他”项。按不合格点的频数由大到小顺序排列个检查项目,“其他”项排在最后。以全部不合格点数为总数,计算各项的频率和累计频率,结果见教材142页表7-6。
(2)排列图的绘制
1)画横坐标。将横坐标按项目数等分,并按项目频数由大到小顺序从左至右排列,该例中横坐标分为六等份。
2)画纵坐标。左侧的纵坐标表示项目不合格点数即频数,右侧纵坐标表示累计频率。要求总频数对应累计频率100%。该例中150应与100%在一条水平线上。
3)画频数直方形。以频数为高画出各项目的直方形。
4)画累计频率曲线。从横坐标左端点开始,依次连接各项目直方形右边线及所对应的累计频率值的交点,所得的曲线即为累计频率曲线。
5)记录必要的事项。如标题、收集数据的方法和时间等。
图7-4为本例混凝土构件尺寸不合格点排列图。
3 .排列图的观察与分析
(1)观察直方形,大致可看出各项目的影响程度。排列图中的每个直方形都表示一个质量问题或影响因素。影响程度与各直方形的高度成正比。
(2)利用abc分类法,确定主次因素。将累计频率曲线按(0%—80%)、 (80%—90%)、(90%—100%)分为三部分,各曲线下面所对应的影响因素分别为a、b、c三类因素。该例中a类即主要因素是表面平整度(2m长度)、截面尺寸(梁、柱、墙板、其他构件),b类即次要因素是水平度,c类即一般因素有垂直度、标高和其他项目。综上分析结果,下部应重点解决a类质量问题。
4 .排列图的应用
排列图可以形象、直观地反映主次因素。其主要应用有:
(1)按不合格点的内容分类,可以分析出造成质量问题的薄弱环节。
(2)按生产作业分类,可以找出生产不合格品最多的关键过程。
(3)按生产班组或单位分类,可以分析比较各单位技术水平和质量管理水平。
(4)将采取提高质量措施前后的排列图对比,可以分析措施是否有效。
(5)此外还可以用于成本费用分析、安全问题分析等。
[ 例题 ] : 排列图法是利用排列图寻找影响质量主次因素的一种有效方法。实际应用中,通常按累计频率划分为三部分,与其对应的影响因素分别为a、b、c三类,其中a类是指( )。
a. 0%—60% b. 0%—80% c. 80%—90% d. 90%-100% 答案:b
四、因果分析图法
1 .因果分析图的概念
因果分析图法是利用因果分析图来系统整理分析某个质量问题(结果)与其产生原因之间关系的有效工具。因果分析图也称特性要因图,又因其形状常被称为树枝图或鱼刺图。
从图7—5可见,因果分析图由质量特性(即质量结果指某个质量问题)、要因(产生质量问题的主要原因)、枝干(指一系列箭线表示不同层次的原因)、主干(指较粗的直接指向质量结果的水平箭线)等所组成。
2 .因果分析图的绘制
下面结合实例加以说明。 图7-5 因果分析图的基本形式
[ 例 7-3]:绘制混凝土强度不足的因果分析图。
因果分析图的绘制步骤与图中箭头方向恰恰相反,是从“结果”开始将原因逐层分解的,具体步骤如下:
(1)明确质量问题—结果。该例分析的质量问题是“混凝土强度不足”,作图时首先由左至右画出一条水平主干线,箭头指向一个矩形框,框内注明研究的问题,即结果。
(2)分析确定影响质量特性大的方面原因。一般来说,影响质量因素有五大方面,即人、机械、材料、方法、环境等。另外还可以按产品的生产过程进行分析。
(3)将每种大原因进一步分解为中原因、小原因,直至分解的原因可以采取具体措施加以解决为止。
(4)检查图中的所列原因是否齐全,可以对初步分析结果广泛征求意见,并作必要的补充及修改。
(5)选择出影响大的关键因素,做出标记“△”。以便重点采取措施。
图7—6是混凝土强度不足的因果分析图。
3 .绘制和使用因果分析图时应注意的问题
(1)集思广益。绘制时要求绘制者熟悉专业施工方法技术,调查、了解施工现场实际条件和操作的具体情况。要以各种形式,广泛收集现场工人、班组长、质量检查员、工程技术人员的意见,集思广益,相互启发、相互补充,使因果分析更符合实际。
(2)制订对策。绘制因果分析图不是目的,而是要根据图中所反映的主要原因,制订改进的措施和对策,限期解决问题,保证产品质量。具体实施时,一般应编制一个对策计划表。
第七章 工程质量控制的统计分析方法 第三节 直方图法、控制图法与相关图法
一、直方图法 (一)直方图的用途 直方图法即频数分布直方图法,它是将收集到的质量数据进行分组整理,绘制成频数分布直方图,用以描述质量分布状态的一种分析方法,所以又称质量分布图法。
通过直方图的观察与分析,可了解产品质量的波动情况,掌握质量特性的分布规律,以便对质量状况进行分析判断。同时可通过质量数据特征值的计算,估算施工生产过程总体的不合格品率,评价过程能力等。
(二)直方图的绘制方法 1. 收集整理数据
用随机抽样的方法抽取数据,一般要求数据在50个以上。
[ 例 7-4] : 某建筑施工工地浇筑c30混凝土,为对其抗压强度进行质量分析,共收集了50份抗压强度试验报告单,经整理如教材145页表7-8。 2.计算极差r极差r是数据中最大值和最小值之差,本例中: xmax=46.2n/mm2 xmin=31.5n/mm2 r=xmax-xmin=46.2-31.5=14.7n/mm2
3 .对数据分组 包括确定组数、组距和组限。 (1)确定组数k。确定组数的原则是分组的结果能正确地反映数据的分布规律。组数应根据数据多少来确定。组数过少,会掩盖数据的分布规律;组数过多,使数据过于零乱分散,也不能显示出质量分布状况。一般可参考表7-9的经验数值确定。
本例中取k=8 (2)确定组距h,组距是组与组之间的间隔,也即一个组的范围。各组距应相等,于是有: 级差≈组距×组数 即 r≈h·k 因而组数、组距的确定应结合级差综合考虑,适当调整,还要注意数值尽量取整,使分组结果能包括全部变量值,同时也便于以后的计算分析。 本例中: h=r/k=14.7/8=1.8≈2n/mm2 (3)确定组限。每组的最大值为上限,最小值为下限,上、下限统称组限。确定组限时应注意使各组之间连续,即较低组上限应为相邻较高组下限,这样才不致使有的数据被遗漏。对恰恰处于组限值上的数据,其解决的办法由二:一是规定每组上(或下)组限不计在该组内,而计入相邻较高(或较低)组内;二是将组限值较原始数据精度提高半个最小测量单位。 本例采取第一种办法划分组限,即每组上限不计入该组内 首先确定第一组下限: xmin-h/2=31.5-2.0/2=30.5第一组上限:30.5+h=30.5+2=32.5第二组下限=第一组上限=32.5第二组上限:32.5+h=32.5+2=34.5以下依次类推,最高组限为44.5~46.5,分组结果覆盖了全部数据。
4. 编制数据频数统计表 统计各组频数,可采用唱票形式进行,频数总和应等于全部数据个数。本例频数统计结果见教材146页表7-10。
5 .绘制频数分布直方图 (三)直方图的观察与分析 1. 观察直方图的形状、判断质量分布状态 作完直方图后,首先要认真观察直方图的整体形状,看其是否是属于正常型直方图。正常型直方图就是中间高,两侧底,左右接近对称的图形,如教材147页图7-8(a)所示。 出现非正常型直方图时,表明生产过程或收集数据作图有问题。这就要求进一步分析判断,找出原因,从而采取措施加以纠正。凡属非正常型直方图,其图形分布有各种不同缺陷,归纳起来一般有五种类型,如教材147页图7-8所示。
(1)折齿型(图7—8(b)),是由于分组组数不当或者组距确定不当出现的直方图。 (2)左(或右)缓坡型(图7—8(c)),主要是由于操作中对上限(或下限)控制太严造成的。
(3)孤岛型(图7—8(d)),是原材料发生变化,或者临时他人顶班作业造成的。
(4)双峰型(图7—8(e)),是由于用两种不同方法或两台设备或两组工人进行生产,然后把两方面数据混在一起整理产生的。
(5)绝壁型(图7—8(f)),是由于数据收集不正常,可能有意识地去掉下限以下的数据,或是在检测过程中存在某种人为因素所造成的。
[
例题 ] :由于分组不当或者组距确定不当出现的直方图是( )型。
a. 折齿型 b. 孤岛型 c. 右缓坡型 d. 双峰型
答案:a
2. 将直方图与质量标准比较,判断实际生产过程能力
作出直方图后,除了观察直方图形状,分析质量分布状态外,再将正常型直方图与质量标准比较,从而判断实际生产过程能力。正常型直方图与质量标准相比较,一般有如教材148页图7—9所示六种情况。图7—9中:
t—表示质量标准要求界限;
b—表示实际质量特性分布范围。
(1)图7—9(a),b在t中间,质量分布中心 与质量标准中心m重合,实际数据分布与质量标准相比较两边还有一定余地。这样的生产过程质量是很理想的,说明生产过程处于正常的稳定状态。在这种情况下生产出来的产品可认为全都是合格品。
(2)图7—9(b),b虽然落在t内,但质量分布中心 与t的中心m不重合,偏向一边。这样如果生产状态一旦发生变化,就可能超出质量标准下限而出现不合格品。出现这样情况时应迅速采取措施,使直方图移到中间来。
(3)图7—9(c),b在t中间,且b的范围接近了t的范围,没有余地,生产过程一旦发生小的变化,产品的质量特性值就可能超出质量标准。出现这种情况时,必须立即采取措施,以缩小质量分布范围。
(4)图7—9(d),b在t中间,但两边余地太大,说明加工过于精细,不经济。在这种情况下,可以对原材料、设备、工艺、操作等控制要求适当放宽些,有目的地使b扩大,从而有利于降低成本。
(5)图7—9(e),质量分布范围b已超出标准下限之外,说明已出现不合格品。此时必须采取措施进行调整,使质量分布位于标准之内。
(6)图7—9(f),质量分布范围完全超出了质量标准上、下界限,散差太大,产生许多废品,说明过程能力不足,应提高过程能力,使质量分布范围b缩小。
[
例题 ] : 如图7—9(d),b在t中间,但两边余地太大,说明( )。
a. 这样如果生产状态一旦发生变化,就可能超出质量标准下限而出现不合格品b. 生产过程一旦发生小的变化,产品的质量特性值就可能超出质量标准c. 加工过于精细,不经济 d. 已出现不合格品答案:c
二、控制图法
( 一 ) 控制图的基本形式及其用途
控制图又称管理图。它是在直角坐标系内画有控制界限,描述生产过程中产品质量波动状态的图形。利用控制图区分质量波动原因,判明生产过程是否处于稳定状态的方法称为控制图法。
1 .控制图的基本形式
控制图的基本形式如教材149页图7—10所示。横坐标为样本(子样)序号或抽样时间,纵坐标为被控制对象,即被控制的质量特性值。控制图上一般有三条线:在上面的一条虚线称为上控制界限,用符号ucl表示;在下面的一条虚线称为下控制界限,用符号lcl表示;中间的一条实线称为中心线,用符号cl表示。中心线标志着质量特性值分布的中心位置,上下控制界限标志着质量特性值允许波动范围。
在生产过程中通过抽样取得数据,把样本统计量描在图上来分析判断生产过程状态。如果点子随机地落在上、下控制界限内,则表明生产过程正常处于稳定状态,不会产生不合格品;如果点子超出控制界限,或点子排列有缺陷,则表明生产条件发生了异常变化,生产过程处于失控状态。
2 .控制图的用途
控制图是用样本数据来分析判断生产过程是否处于稳定状态的有效工具。它的用途主要有两个:
(1)过程分析,即分析生产过程是否稳定。为此,应随机连续收集数据,绘制控制图,观察数据点分布情况并判定生产过程状态。
(2)过程控制,即控制生产过程质量状态。为此,要定时抽样取得数据,将其变为点子描在图上,发现并及时消除生产过程中的失调现象,预防不合格品的产生。
前面讲述的排列图、直方图法是质量控制的静态分析法,反映的是质量在某一段时间里的静止状态。然而产品都是在动态的生产过程中形成的,因此,在质量控制中单用静态分析法显然是不够的,还必须有动态分析法。只有动态分析法,才能随时了解生产过程中质量的变化情况,及时采取措施,使生产处于稳定状态,起到预防出现废品的作用。控制图就是典型的动态分析法。
[
例题 ] : 控制图是用样本数据来分析判断生产过程是否处于稳定状态的有效工具。它的用途主要有( )。
a. 过程分析 b. 过程控制 c. 过程判断 d. 过程稳定 e.过程变化
答案:ab
(二)控制图的原理
本章第一节质量数据波动的原因中已讲到,影响生产过程和产品质量的原因,可分为系统性原因和偶然性原因。
在生产过程中,如果仅仅存在偶然性原因影响,而不存在系统性原因,这时生产过程是处于稳定状态,或称为控制状态。其产品质量特性值的波动是有一定规律的,即质量特性值分布服从正态分布。控制图就是利用这个规律来识别生产过程中的异常原因,控制系统性原因造成的质量波动,保证生产过程处于控制状态。
如何衡量生产过程是否处于稳定状态呢?我们知道:一定状态下的生产的产品质量是具有一定分布的,过程状态发生变化,产品质量分布也随之改变。观察产品质量分布情况,一是看分布中心位置(μ);二是看分布的离散程度(σ)。这可通过教材150页图7—11所示的四种情况来说明。图7—11(a),反映产品质量分布服从正态分布,其分布中心与质量标准中心m重合,散差分布在质量控制界限之内,表明生产过程处于稳定状态,这时生产的产品基本上都是合格品,可继续生产。
图7—11(b),反映产品质量分布散差没变,而分布中心发生偏移。
图7—11(c),反映产品质量分布中心虽然没有偏移,但分布的散差变大。
图7—11(d),反映产品质量分布中心和散差都发生了较大变化,即μ值偏离标准中心,σ(s)值增大。后三种情况都是由于生产过程中存在异常原因引起的,都出现了不合格品,生产过程处于不稳定状态,应及时分析,消除异常原因的影响。
综上所述,我们可依据描述产品质量分布的集中位置和离散程度的统计特征值,随时间(生产进程)的变化情况来分析生产过程是否处于稳定状态。在控制图中,只要样本质量数据的特征值是随机地落在上、下控制界限之内,就表明产品质量分布的参数μ和σ基本保持不变,生产中只存在偶然原因,生产过程是稳定的。而一旦发生了质量数据点飞出控制界限之外,或排列有缺陷,则说明生产过程中存在系统原因,使μ和σ发生了改变,生产过程出现异常情况。
(三)控制图的观察与分析
绘制控制图的目的是分析判断生产过程是否处于稳定状态。这主要是通过对控制图上点子的分布情况的观察与分析进行。因为控制图上点子作为随机抽样的样本,可以反映出生产过程(总体)的质量分布状态。
当控制图同时满足以下两个条件:一是点子几乎全部落在控制界限之内;二是控制界限内的点子排列没有缺陷。我们就可以认为生产过程基本上处于稳定状态。如果点子的分布不满足其中任何一条,都应判断生产过程为异常。
(1)点子几乎全部落在控制界线内,是指应符合下述三个要求:
1)连续25点以上处于控制界限内。
2)连续35点中仅有1点超出控制界限。
3)连续100点中不多于2点超出控制界限。
(2)点子排列没有缺陷,是指点子的排列是随机的,而没有出现异常现象。这里的异常现象是指点子排列出现了“链”、“多次同侧”、“趋势或倾向”、“周期性变动”、“接近控制界限”等情况。
1)链。是指点子连续出现在中心线一侧的现象。出现五点链,应注意生产过程发展状况。出现六点链,应开始调查原因:出现七点链,应判定工序异常,需采取处理措施,如教材151页图7—12(a)所示。
2)多次同侧。是指点子在中心线一侧多次出现的现象,或称偏离。下列情况说明生产过程已出现异常:在连续11点中有10点在同侧,如教材151页图7—12(b)所示。在连续14点中有12点在同侧。在连续17点中有14点在同侧。在连续20点中有16点在同侧。
3)趋势或倾向。是指点子连续上升或连续下降的现象。连续7点或7点以上上升或下降排列,就应判定生产过程有异常因素影响,要立即采取措施,如教材151页图7—12(c)所示。
4)周期性变动。即点子的排列显示周期性变化的现象。这样即使所有点子都在控制界限内,也应认为生产过程为异常,如教材151页图7—12(d)所示。
5)点子排列接近控制界限。是指点子落在了μ±2,以外和μ±3σ以内。如属下列情况的判定为异常:连续3点至少有2点接近控制界限。连续7点至少有3点接近控制界限。连续10点至少有4点接近控制界限。如教材151页图7—12(e)所示。
以上是分析用控制图判断生产过程是否正常的准则。如果生产过程处于稳定状态,则把分析用控制图转为管理用控制图。分析用控制图是静态的,而管理用控制图是动态的。随着生产过程的进展,通过抽样取得质量数据把点描在图上,随时观察点子的变化,一是点子落在控制界限外或界限上,即判断生产过程异常,点子即使在控制界限内,也应随时观察其有无缺陷,以对生产过程正常与否做出判断。
三、相关图法 ( 一 ) 相关图法的用途
相关图又称散布图。在质量控制中它是用来显示两种质量数据之间关系的一种图形。质量数据之间的关系多属相关关系。一般有三种类型:一是质量特性和影响因素之间的关系;二是质量特性和质量特性之间的关系;三是影响因素和影响因素之间的关系。
我们可以用y和x分别表示质量特性值和影响因素,通过绘制散布图,计算相关系数等,分析研究两个变量之间是否存在相关关系,以及这种关系密切程度如何,进而对相关程度密切的两个变量,通过对其中一个变量的观察控制,去估计控制另一个变量的数值,以达到保证产品质量的目的。这种统计分析方法,称为相关图法。
[
例题 ] :在质量控制中( )是用来显示两种质量数据之间关系的一种图形。
a. 排列图 b. 直方图 c. 控制图 d. 相关图
答案:d
( 二 ) 相关图的绘制方法
[ 例 7-5] : 分析混凝土抗压强度和水灰比之间的关系。
1 .收集数据
要成对地收集两种质量数据,数据不得过少。本例收集数据如教材152页表7—11所示。
2 .绘制相关图
在直角坐标系中,一般x轴用来代表原因的量或较易控制的量,本例中表示水灰比;y轴用来代表结果的量或不易控制的量,本例中表示强度。然后将数据中相应的坐标位置上描点,便得到散布图,如教材152页图7-13所示。
( 三 ) 相关图的观察与分析
相关图中点的集合,反映了两种数据之间的散布状况,根据散布状况我们可以分析两个变量之间的关系。归纳起来,有以下六种类型,如教材153页图7-14所示。
(1)正相关(图7-14a)。散布点基本形成由左至右向上变化的一条直线带,即随x增加,y值也相应增加,说明x与y有较强的制约关系。此时,可通过对x控制而有效控制y的变化。
[
例题 ] :散布点基本形成由左至右向上变化的一条直线带,即随x增加,y值也相应增加, x与y有较强的制约关系,这种相关图是( )。
a. 正相关 b. 弱正相关 c. 不相关 d. 负相关
答案:a
(2)弱正相关(图7—14b)。散布点形成向上较分散的直线带。随x值的增加,y值也有增加趋势,但x、y的关系不像正相关那么明确。说明y除受x影响外,还受其他更重要的因素影响。需要进一步利用因果分析图法分析其他的影响因素。
(3)不相关(图7-14c)。散布点形成一团或平行于x轴的直线带。说明x变化不会引起y的变化或其变化无规律,分析质量原因时可排除x因素。
(4)负相关(图7-14d)。散布点形成由左向右向下的一条直线带。说明x对y的影响与正相关恰恰相关。
(5)弱负相关(图7-14e)。散布点形成由左至右向下分布的较分散的直线带。说明x与y的相关关系较弱,且变化趋势相反,应考虑寻找影响y的其他更重要的因素。
(6)非线性相关(图7-14f)。散布点呈一曲线带,即在一定范围内x增加,y也增加;超过这个范围x增加,y则有下降趋势,或改变变动的斜率呈曲线形态。 从图7-14可以看出本例水灰比对强度影响是属于负相关。初步结果时,在其他条件不变的情况下,混凝土强度随着水灰比增大又逐渐降低的趋势。
第四节 抽样检验方案 一、抽样检验的几个基本概念 1 .抽样检验方案 抽样检验方案是根据检验项目特性所确定的抽样数量、接受标准和方法。如在简单的计数值抽样检验方案中,主要是确定样本容量n和合格判定数,.即允许不合格品件数c,记为方案(n,c)。
2. 检验. 检验是对检验项目中的性能进行量测、检查、试验等,并将结果与标准规定要求进行比较,以确定每项性能是否合格所进行的活动。它包括对每一个体的缺陷数目或某种属性记录的计数检验和对每一个体的某个定量特性的计量检验。
3 .检验批 4 .批不合格品率 批不合格品率是指检验批中不合格品数占整个批量的比重。反映了批的质量水平,其计算公式为:由总体计算:p=d/n由样本计算:p=d / n式中 p、p—分别由检验批,(总体)、样本计算的批不合格品率; d、d—分别为检验批、样本中的不合格品件数; n、n—分别为检验批、样本中的产品件数。 对于计点值数据,若用c表示批中的缺陷数时,其质量水平可由下式计算: 批的每百单位缺陷数=100 c/n
5 .过程平均批不合格品率 过程平均批不合格品率是指对k批产品首次检验得到的k个批不合格品率的平均数。它可以衡量一个基本稳定的生产过程,在较长时间内所提供产品的质量水平。由总体计算的用 表示;由样本计算的k批的平均不合格品率用 表示。 是 的优良估计值。这里,首次检验的含义是指:在实施二次或多次抽样检验方案时,只能取第一个样本的p或p值计算;k值不应少手20批。一般利用抽样检验结果计算:公式为
6 . 接受概率 接受概率又称批合格概率;是根据规定的抽样检验方案将检验批判为合格而接受的概率一个既定方案的接受概率是产品质量水平,即批不合格品率p的函数,用l(p)表示,检验批的不合格品率p越小接受概率l(p)就越大。
二、抽样检验方案类型 ( 一 ) 抽样检验方案的分类 抽样检验方案的分类见教材155页图7—15。
(二)常用的抽样检验方案 1. 标准型抽样检验方案 (1)计数值标准型一次抽样检验方案 计数值标准型一次抽样检验方案是规定在一定样本容量n时的最高允许的批合格判定数c,记作(n,c),并在一次抽检后给出判断检验批是否合格的结论。c也可用ac表示。c值一般为可接受的不合格品数,也可以是不合格品率,或者是可接受的每百单位缺陷数。若实际抽检时,检出不合格品数为d,则当: d≤c时,判定为合格批,接受该检验批;d>c定为不合格批,拒绝该检验批。 (2)计数值标准型二次抽样检验方案 计数值标准型二次抽样检验方案时规定两组参数,即第一次抽检的样本容量n1时的合格判定数c1和不合格判定数r1(c1<r1=;第二次抽检的样本容量n2时的合格判定数c2。在最多两次抽检后就能判断检验批是否合格的结论。其检验程序是: 第一次抽检n1后,检出不合格品数为d1,则当: dl≤cl时,接受该检验批;d1≥r1时,拒绝该检验批;c1<dl<rl时,抽检第二个样本。 第二次抽检n2后,检出不合格品是为d2,则当: d1+d2≤c2时,接受该检验批;d1+d2>c2时,拒绝该检验批。以上两种标准型抽样检验程序见教材155页图7-16、图7-17。 (3)多次抽样检验方案
2. 分选型抽样检验方案 计数值分选型抽样检验方案基本与计数值标准型一次抽样检验方案相同,只是在抽检后给出检验批是否合格的判断结论和处理有所不同。即实际抽检时,检出不合格品数为d,则当:d<c时,接受该检验批;d>c时则对该检验批余下的个体产品全数检验。
3. 调整型抽样检验方案 计数值调整型抽样检验方案时在对正常抽样检验的结果进行分析后,根据产品质量的好坏,调整型抽样检验方案加严或放宽的规则详见教材156页图7-18。
三、抽样检验方案参数的确定 实际抽样检验方案中也都存在两类判断错误。即可能犯第一类错误,将合格批判为不合格批,错误地拒收;也可能犯第二类错误,将不合格批判为合格批,错误地接受。错误的判断将带来相应的风险,这种风险的大小可用概率来表示。如教材157页图7-19所示。第一类错误是当p=po时,以高概率l(p)=1-α接受检验批,以α为拒收概率将合格批判为不合格。由于对合格品的错判将给生产者带来损失,所以关于合格质量水平po的概率α,又称供应方风险、生产方风险等。 第二类错误是当p=p1时,以高概率(1-β)拒绝检验批,以β为接受概率将不合格批判为合格。这种错误是将不合格品漏判从而给消费者带来损失,所以关于极限不合格质量水平p1的概率β,又称使用方风险、消费者风险等。以下叙述均以技术指标准型一次抽样方案为例。
( 一 ) 确定 α 与 β 如前所述,α是生产者所要承担的风险,β是使用者所要承担的风险;生产者特别要防止质量合格的产品错被拒收;反之,使用者则力求避免或减少接收质量不合格的产品,双方都希望尽量减小自己的损失。要绝对避免这两种错判是不可能的,片面强调某一方的利益也是不对的。一个合理有效的抽样检验方案应该是将两类风险都控制在一个适当小的范围内,尽量减少所带来的损失。 为了保护消费者和生产者的利益,一般都有一定的规定和标准,也可以双方协商确定。《建筑工程施工质量验收统一标准》中的规定是:在抽样检验中,两类风险一般控制范围是α=1%~5%;β=5%~10%。对于主控项目,其α、β均不宜超过5%;对于一般项目,α不宜超过5%,β不宜超过10%。
( 二 ) 确定 p 0 (aql) 与 p 1 (ltpd) 1 .应考虑的因素 p0 (aql)是生产者比较重视的参数,p1 (ltpd)是使用者比较重视的参数,它们是制定抽样检验方案的基础,因此要综合考虑各方面因素的影响慎重确定。其主要方面有: (1)确定p0、p1应以α、β为标准。 (2)生产过程的质量水平,即过程平均批不合格品率 的大小。(3)质量要求及不合格品对使用性能的影响程度。(4)制造成本和检查费用。
2 .确定 p 0 一般由使用方和供应方协商确定;还可计算检验盈亏点pb确定p0,计算公式为: 检验盈亏点pb =检验一件产品的成本(α)/一件不合格品造成的损失(b) pb值越小表示产品质量问题越严重,造成损失越大。 对于致命缺陷、严重缺陷、p0值应取得小些p0=0.1%、0.3%、0.5%等;对于轻微缺陷,出于经济考虑,p0值可取得大些:p0=3%、5%、10%等。
3 .确定 p 1 抽样检验方案中,p1与p0的比例常用鉴别比p1/ p0表示,鉴别比值过小,如p1/ p0≤3时,会因增加抽检数量n而使检验费用增加;鉴别比值过大,如p1/p0>20时,又会放松对质量的要求,对用户不利。通常是以α=5%、β=10%为准,取p1=(4-lo)po。
( 三 ) 确定抽样检验方案( n , c ) 根据α、β与p0、p1和p1/p0可通过公式计算、查图、查表得到n,c数值。至此,抽样检验方案即已确定。以下仅介绍利用一次抽样检验表见教材158页(表7-12)求参数n,c的方法。
[ 例 7-7]: 设α=0.05,β=0.10,p0=0.01,p1=0.07,求一次抽样检验方案(n,c)。 计算鉴别比p1/ p0=0.07/0.01=7; 查表 α=0.05,β=0.01栏内最接近的值为6.509; 查表 6.509对应c的值是2,对应的n p0为0.818; 于是有:n p0/ p0=0.818/0.01=82 即所求一次抽样检验方案(82,2)。抽样检验方案确定后,既可采用选定的抽样方法(分类抽样、等距抽样、整群抽样等),从既定的检验批中随机抽取n件样品,按照质量标准进行检验和判断。
本文标题:
质量工程师考试-2003年质量工程师资格考试考题精选一 本文地址:
http://www.61k.com/1125232.html