一 : 17SDYSC-1山地运输车传动系统的设计
摘 要
我国山区面积巨大,山区由于地形崎岖,交通闭塞,经济文化落后。尤其是在我国西部山区,不通公路的山区较多,运输能力差,无法实现物流的畅通,难以适应市场经济的发展,制约山区农村经济的发展。
为了解决山地间的货物运输,我们尝试设计一种山地运输车,使其具备良好的山地运行特性,能够在山区复杂路面行驶。同时,具有强大的爬坡性能,体积小巧,运输能力强,可基本满足山区运输的需要。这样,就可以解决山区筑路困难无法运输的问题。车辆设计长度小于2500mm,宽度小于1200mm,载重2吨,爬坡能力不大于45度,主要用于山地间的普通货物运输。
本设计为SDYSC-1山地运输车传动系统设计,是在山地运输车总体设计的基础上完成的。车辆的传动系统是从发动机到驱动轮之间所有的动力传递装置的总称。山地运输车的传动系统是整个运输车的核心关键部分,其直接决定了山地运输车的性能,在整车设计中非常重要。本设计根据设计要求及总体设计的相关数据,根据经济、适用、安全可靠的设计原则和分析比较,首先完成了传动系统总体方案的确定。之后从柴油发动机的选择开始,一步步确定了各液压传动部件的主要参数,最后完成了行星减速器及零部件的设计计算。
通过本课题的研究与设计,巩固和扩大学生在校期间所学的基础知识与专业知识,对培养学生的实际工作能力。设计出了车辆的传动系统,满足了山地运输车经济、实用、可靠的条件。
关键词:山地运输车; 履带式; 传动系统;行星减速器
ABSTRACT Our country has great mountainous area and rugged mountainous area, because the traffic block, the economy and culture development is relatively slow. Especially in the western
mountainous area, most of the mountain area does not have highway, the transportation ability is poor, therefore cannot achieve logistics flow, difficult to adapt to the development of market economy, and restricted the economic development of rural and mountainous areas.
In order to solve the transport of goods between the mountain terrain, we try to design a mountain truck, which have good mountain operation characteristic, can run on the complex mountains road. At the same time, the truck should be small, have a strong ability of climbing and transportation, thus satisfy the basic need of mountain transportation. In this way, it can solve the transportation problem in mountain area. The vehicle’s length and width should less than 2500 mm and 1200 mm respectively, carrying ability is 2 tons, and climbing ability is not more than 45 degrees, mainly use for the ordinary transport between hill area.
This design is SDYSC-1 mountain truck driving system which based on the overall design of mountain area transportation. Vehicle transmission system is defined as the whole power transfer device from engine and drive round. The transmission system is the core of the vehicle because it directly determines the performance of the vehicle, so in the vehicle design it is very important. According to the design requirements, overall of relevant data, economic, applicable, safety, reliable design principles, analysis and comparison, this design first complete
transmission system. After that we start from the choice of diesel engine, identify various main parameters of the hydraulic transmission parts step by step, and finally completed a planetary reducer and components design calculation.
This project and design consolidate and expand the students’ basic and professional knowledge learned in school and contribute a lot to students' practical ability to work. In addition it designed a vehicle transmission system, which is economy, practical and reliable, could satisfy the mountain area transportation.
Key words:Mountain; Truck caterpillar; Planetary reducer; Transmission system
目 录
1前 言 ............................................................................................................................................................... 5
2山地运输 ........................................................................................................................................................... 5
2.1山地运输的现状 .................................................................................................................................... 5
2.1.1汽车运输 ..................................................................................................................................... 5
2.1.2中小型拖拉机和农用运输车 ..................................................................................................... 6
2.1.3全地形履带运输车 ..................................................................................................................... 6
2.2发展趋势 ................................................................................................................................................ 6
2.3山地运输车行走装置应满足的要求 .................................................................................................... 7
3传动系统总体方案的确定 ............................................................................................................................... 7
3.1动力装置的选择 ................................................................................................................................... 7
3.1.1电动机 ......................................................................................................................................... 7
3.1.2柴油机 ......................................................................................................................................... 7
3.1.3蒸汽机 ......................................................................................................................................... 7
3.2传动方式的比较与选择 ........................................................................................................................ 8
3.2.1机械传动 ..................................................................................................................................... 8
3.2.2液力机械传动 ............................................................................................................................. 8
3.2.3电力传动 ..................................................................................................................................... 9
3.2.4液压传动 ..................................................................................................................................... 9
3.2.5比较选择 ..................................................................................................................................... 9
3.3总体传动方案 ...................................................................................................................................... 10
4传动系统主要参数的确定 ............................................................................................................................. 10
4.1柴油发动机的参数 .............................................................................................................................. 10
4.2行走装置的参数 ...................................................................................................................................11
4.3行走装置的牵引力计算 .......................................................................................................................11
4.3.1土壤的变形阻力 ........................................................................................................................11
4.3.2坡度阻力 ....................................................................................................................................11
4.3.3转弯阻力 ....................................................................................................................................11
4.3.4履带运行的内阻力 ................................................................................................................... 12
4.3.5不稳定运行时的惯性阻力 ....................................................................................................... 12
4.3.6总阻力的计算 ........................................................................................................................... 12
4.3.7牵引力的校核 ........................................................................................................................... 12
4.4液压马达主要参数计算确定 .............................................................................................................. 13
4.4.1液压马达输出功率 ................................................................................................................... 13
4.4.2液压马达最高输出转速 ........................................................................................................... 13
4.4.3液压马达的输出力矩 ............................................................................................................... 14
4.4.4马达理论排量 ........................................................................................................................... 14
5行星齿轮减速器的设计 ................................................................................................................................. 15
5.1行星齿轮传动的特点和优越性 .......................................................................................................... 15
5.1.1行星齿轮传递的优越性 ........................................................................................................... 15
5.1.2行星齿轮传动的优越性 ........................................................................................................... 15
5.2行星减速器传动方案的选定和传动比的分配确定原则 .................................................................. 16
5.2.1行星减速器传动方案的选定 ................................................................................................... 16
5.2.2传动比的分配确定原则 ........................................................................................................... 16
5.3行星减速器齿轮配齿与计算 .............................................................................................................. 17
5.3.1传动比公式的推导 ................................................................................................................... 17
5.3.2行星排齿轮的配齿 ................................................................................................................... 17
5.3.3行星齿轮模数计算与确定 ....................................................................................................... 18
5.4啮合参数计算 ...................................................................................................................................... 19
5.4.1第Ⅰ行星排的中心距 ............................................................................................................... 19
5.4.2第Ⅱ行星排的中心距 ............................................................................................................... 20
5.4.3变位系数的选取 ....................................................................................................................... 20
5.5各行星齿轮几何尺寸计算 .................................................................................................................. 21
5.5.1第Ⅰ排行星齿轮的几何尺寸 ................................................................................................... 21
5.5.2第Ⅱ排行星轮的几何尺寸 ....................................................................................................... 23
5.6各行星齿轮强度校核 .......................................................................................................................... 25
5.6.1太阳轮和行星轮接触疲劳强度校核 ....................................................................................... 25
5.6.2太阳轮和行星轮弯曲疲劳强度校核 ..................................................................................... 27
5.6.3内齿轮材料选择 ....................................................................................................................... 28
5.7减速器结构的设计 .............................................................................................................................. 29
5.7.1齿轮轴的设计计算 ................................................................................................................... 29
5.7.2传递连接 ................................................................................................................................... 30
5.7.3轴承选用与校核 ....................................................................................................................... 30
5.7.4其他附件说明 ........................................................................................................................... 31
6结 论 ............................................................................................................................................................. 31
参考文献 ............................................................................................................................................................ 33
致谢 .................................................................................................................................................................... 34
1前 言
我国山区面积占全国总面积的三分之二以上,广大山区有着丰富的森林和矿产资源,为发展经济提供雄厚的物质基础。但是山区往往由于地形崎岖,不通公路,交通闭塞,运输能力差,无法实现物流的畅通,经济文化常常相对落后,运输问题很大程度上制约着山区经济的发展。
本设计就是为了解决山区间简单的运输问题,来源于生产。此山地运输车,具备良好的山地运行特性,具有强大的爬坡性能,能够在山区复杂路面行驶。同时,体积小巧,运输能力强,整机结构简单,维修和保养方便,便于操纵,具备良好的通过性和适用性,可基本满足山区运输的需要。
本设计题目为《SDYSC-1山地运输车传动系统设计》,故说明书主要介绍了此种山地运输车传动系统的设计。该设计结合机械专业的教学内容和国内外相关设备应用与发展。对小型履带式山地运输车传动系统进行了较深入的分析研究。本设计依据设计要求和总体设计方案及参数完成,同时遵循以下原则:满足使用要求,具有良好的爬坡和转向性能;整体布置、外形尺寸方便合理,具有良好的通过性;设计满足结构和工艺要求,符合机械行业设计标准;满足基本的安全性和稳定性。在以上设计标准、原则下,本设计具体完成了:山地运输车传动系统总体方案的确定,液压传动各部件参数的计算以及行星减速器的设计。
通过毕业设计,使我们进一步掌握机械设计的方法和步骤,巩固、加深对所学的基础理论、基本技能。训练了我们调查研究、查阅文献、收集资料并进行分析的能力,制订设计方案的能力,产品设计与开发能力;设计、计算和绘图能力;书面及口头表达能力,动手实践能力及外语水平等。巩固和扩大在校期间所学的基础知识与专业知识,接受了工程师必须的综合训练,对培养实际工作能力具有巨大的作用。
2山地运输
2.1山地运输的现状
目前应用于山地运输的车辆种类繁多,以下列举的一些典型运输设备的概况和优缺点。
2.1.1汽车运输
汽车运输是解决一般道路运输问题最普遍的运输方式。与其他运输方法相比,汽车运输方法在运输方案制定与实施、运输车辆装载能力等方面有相当巨大的优势。但是,山地丘陵地区的路面主要为中级沙石路面和低级泥结碎石或土路,普通的汽车运输车辆无法安全通畅的在此类道路上行驶。为此需要修建公路和基础设施,而修建能供现有运输车辆运行的道路,其难度较大,耗费资金巨大,山区经济实力差,无法承受。
目前解决汽车在山区运输的主要方法是,利用已有道路,适当拓宽少数汽车无法通行的窄道,新开辟修整少量小路,最大限度减少施工现场运输对环境和植被的破坏,降低道路施工的总工程量,降低成本,可完成一些基本的山地运输任务。
17SDYSC-1山地运输车传动系统的设计_7sdy
2.1.2中小型拖拉机和农用运输车
此类农用机械一般用于农用生产和运输,能够适应窄路和急弯等较复杂路况,同时具有一定的爬坡能力,完全可以完成一般的山区运输任务。但是,由于不是专用的山地运输车辆,所以其车辆装载能力有限,在面对山区陡坡时的爬坡能力有限。尤其是南方某些地方,其山区雨季道路泥泞不堪,路面情况复杂多变,工作环境不稳地,运输条件极其恶劣。在此类情况下,这种一般的农用运输车辆无法保证在山路的安全行驶,无法完成运输任务。
2.1.3全地形履带运输车
全地形车运输车可以在任何地形上行驶,如沼泽、雪地、山林、池塘、溪流等恶劣的地形,可以完成普通车辆难以行驶的非公路路况下,人员、货物运输或抢险救灾任务。履带运输车完全可以适应山区的道路情况,即使在最复杂、最恶劣的行驶条件下,同样可以进行作业。更重要的是,此类车辆具有良好的可操纵性,同时稳定行性方面较其他运输设备具有很大的优势。
虽然履带车辆使用环境多变,但是由于其本身机械系统非常复杂,加大了设计和制造的成本,人们负担能力有限。而且,有些山区道路狭窄,路面情况复杂,陡坡及松软路面多。而一般的履带运输车,车身重、体积大,车辆在机动灵活性及狭窄复杂地形通过能力方面扔有待提高。
图1 履带式山地运输车
2.2发展趋势
现有的运输车辆都具有一定的局限性,无法顺利全面的完成山地运输任务。为了解决这样的问题,新型的山地运输车,首先必须其具备出色良好的山地运行特性,能够在山区复杂路面安全、平稳的行驶。同时,必须具有强大的爬坡性能,面对山区陡坡及松软路面依然可以行使。车辆体积方面,设计要小巧灵活,同时保证装载能力,使其既拥有出色灵活性和通过能力,又具有良好的运输
能力,这样就可基本满足山区运输的需要。将这样的山地运输车用于山区运输,既大幅度降低修建
道路的难度和耗费的资金,又可以解决山区运输筑路难的问题,有利于提高山区人民生活质量和发展山区农村的经济水平。
2.3山地运输车行走装置应满足的要求
对于整个山地运输车最为重要的行走装置,在设计时应满足下列要求:
⑴驱动力:要有较大的驱动力,使其在湿软或高低不平具有良好的爬坡性能和转向性能。 ⑵通过性:在不增大行走装置高度的前提下使其具有较大的离地间隙,以提高其不平地面上的越野性能。
⑶稳定性:行走装置具有较大的支撑面积或较小的接地比压,以提高稳定性。 ⑷安全性:机械在斜坡下行时不发生下滑和超速溜坡现象,以提高安全性。 ⑸方便性:行走装置的外形尺寸应符合道路运输的要求。
3传动系统总体方案的确定
3.1动力装置的选择
工程机械上常用的动力装置主要有三种:电动机、柴油机以及蒸汽机,下面是三种动力装置源的概况和特点:
3.1.1电动机
电动机是一种旋转式电动机器,它将电能转变为机械能。电动机能提供的功率范围很大,从毫瓦级到万千瓦级。电动机的使用和控制非常方便,具有自起动、加速、制动、反转、掣住等能力,能满足各种运行要求;电动机的工作效率较高,又没有烟尘、气味,不污染环境,噪声也较小。由于它的一系列优点,所以在工农业生产、交通运输、国防、商业及家用电器、医疗电器设备等各方面广泛应用。
3.1.2柴油机
柴油机是用柴油作燃料的内燃机,属于压缩点火式发动机。柴油机具有热效率高的显著优点,经济性优于汽油机,功率大,符合工程机械向大型化发展的趋势。其应用范围越来越广。柴油机具有较好的燃油经济性,使用成本低,在相同的续驶里程内,可以设置容积小些的油箱。柴油机工作可靠,寿命长,排污量少。随着强化程度的提高,柴油机单位功率的重量也显著降低。为了节能,各国都在注重改善燃烧过程,研究燃用低质燃油和非石油制品燃料。此外,降低摩擦损失、广泛采用废气涡轮增压并提高增压度、进一步轻量化、高速化、低油耗、低噪声和低污染。
3.1.3蒸汽机
蒸汽机是将蒸汽的能量转换为机械功的往复式动力机械。蒸汽机的出现曾推动了机械工业甚至社会的发展,现代蒸汽机的最大的优点是它几乎可以利用所有的燃料将热能转化为机械能。但是蒸汽机离不开锅炉,整个装置既笨重又庞大。而且它是一种往复式机器,惯性力限制了转速的提高;工作过程是不连续的,蒸汽的流量受到限制,也就限制了功率的提高。逐渐为其他动力装置所代替。
综上所述几类动力装置的特点,设计的山地运输车主要在山路间行驶,同时需要较大的功率的动力源。柴油机作为动力装置不受电源、电缆的限制,行驶方便,符合工程机械动力装置的需要,故本设计采用了柴油机作为动力装置。
3.2传动方式的比较与选择
传动系统是从发动机到驱动轮之间所有的动力传递装置的总称。传动系统的功用是把动力装置输出的功率传递给驱动轮,并改变动力装置的输出特性,以满足对自行式工程机械车速和牵引力的要求。目前,工程机械的传动系统有以下四种类型:机械传动、液力机械传动、电力传动以及液压传动。
3.2.1机械传动
机械传动是指传动系统中采用刚性零部件传递动力的方式。它是通过齿轮、齿条、带、链等机件传递动力和进行控制。工程机械中使用机械传动系统由来已久。机械传动具有结构简单、制造容易、工作可靠、重量轻、操作简单、维护方便、价格低廉、传动效率高、可以利用传动系统运动零件的惯性进行作业等优点。但是机械传动存在许多缺点:
⑴在行驶阻力急剧变化的工况下,柴油机容易过载熄火,因此要求司机有熟练的操作技巧。 ⑵采用机械式变速箱,换挡时动力中断时间长。
⑶柴油机振动直接传递到传动系个零件,而行驶阻力的变动又直接影响柴油机的工作,降低了柴油机和零部件的使用寿命。
⑷工作阻力的变化将直接影响发动机的工作,为了充分利用发动机的功率,需要增加变速器的档位数,因而变速器结构变得复杂,并且增加了司机的换档次数。
⑸机械传动不能进行无极调速,远距离传动比较困难。
上述缺点在行驶阻力变化剧烈及经常改变行驶方向的工况下影响特别显著。因此,机械传动适用于行驶阻力比较稳定的连续作业机械。
3.2.2液力机械传动
液力机械传动是在普通机械传动系统中串联或并联加入液力变矩器(或液力偶合器)后,使发动机输出的动力通过液力变矩器(或液力偶合器)及机械传动部件传到驱动轮,这个系统称为液力机械传动系统。它具有的主要优点是:使工程机械具有自动适应载荷变化的特性;简化了机械的操纵,延迟了机械的使用寿命;提高了机械的起步性能和通过性能同时简化了维修工作。
与机械传动相比,液力机械传动的主要缺点是成本高,在行驶阻力变化小而进行连续作业时,上述优点并不明显,而由于变矩器的传动损失,增加的燃油消耗量。
3.2.3电力传动
电力传动是利用电力设备并调节电参数来传递动力和进行控制。采用发电机驱动发电机发电,通过电力驱动电动机,进而驱动行走机构与工作机构。电力传动的主要优点是:
⑴动力装置和车轮之间无刚性联系,便于总体布置和维修。 ⑵变速箱操纵轻便,可实现无级变速,同时容易实现自动操作。
⑶电动轮通用性强,可简单的实现任意多驱动轮的方式以满足不同机械对牵引性能和通过性能的要求。
电力传动存在的缺点是:运动平稳性差,易受外界负载的影响,惯性大,起动及转向慢,受温度、湿度、振动、腐蚀等环境因素影响较大。而且成本高,据统计比液力机械传动成本约贵20%左右。目前仅用于大功率的自卸载重汽车、铲运机及矿用轮式装载机等机械中。
3.2.4液压传动
采用发动机驱动随机的油泵站,再由液压马达驱动行走机构。该传动方式取消了主离合器、变速箱、后桥等传动部件,使工作装置的操纵和整机驱动方式统一,可减轻机重、结构紧凑、总体布置简单,原地转向性能好,可实现牵引力和速度的无极调整,大大提高了牵引性能。与其它传动方式相比,液压传动具有的有点有:
⑴能实现无级变速且变速范围大,并能实现微动。 ⑵变速操纵简单。
⑶可利用液压系统实现制动。
⑷采用左右轮分别驱动的系统,能方便地实现弯道行驶和转向。 ⑸便于实现自动和远距离操作。
液压传动具有其独特的优越性,但也不能忽视其存在的缺点:对液压元件制造精度要求高,工艺复杂,成本较高;液压元件维修较复杂,且需有较高的技术水平;液压传动对油温变化较敏感,这会影响它的工作稳定性。因此液压传动不宜在很高或很低的温度下工作,使用液压传动对维护的要求高,工作油要始终保持清洁。液压传动在能量转化的过程中,压力大,流量损失大,系统传动效率较低。
3.2.5比较选择
下页表1中列举了几种传动方式的主要特性的比较。经过以上分析比较,同时考虑到液压技术不断完善,液压传动的应用日益广泛。根据本山地运输车的实际要求和具体情况,在充分考虑其实现可行性和经济性的基础上,此山地运输侧的传动系统采用液压传动系统。
表1 几种传动方式的主要传动特性比较
特性及性能 功能与重量比 转矩与转动惯量比
响应速度 可控性 负载刚度 调速范围
机械传动
小 小 低 差 中等 小
电力传动
小 小 中等 中等 差 中等
液压传动
大 大 高 好 大 大
3.3总体传动方案
由于总体设计上,山地运输车采用的行走方式为履带式行走装置,结合上述传动系统的具体方案,最终确定整个山地运输车的行走装置动力路线为:柴油机—液压泵—控制阀—液压马达—制动器—减速器—驱动轮—履带。
4传动系统主要参数的确定
4.1柴油发动机的参数
参考近似工程机械的设计参数,结合本山地运输车的具体工作条件和整体设计要求,拟选取常柴ZN490QA多缸柴油机。主要技术参数如表2:
发动机型式 汽缸数 缸径(mm) 冲程(mm) 总排量(L)
标定功率/转速(kW/r/min) 最大转矩/转速(N.m/r/min)
喷射方式 进气方式 外形尺寸(mm) 静质量(kg)
直列—水冷—4冲程
4 90 95 2.417 41.2/3200 137.8/2240 直喷式 自然吸气 696×492×650
205
17SDYSC-1山地运输车传动系统的设计_7sdy
二 : 电气控制柜工艺设计
1、基本思路
电气控制柜设计的基本思路是一种逻辑思维,只要符合逻辑控制规律、能保证电气安全及满足生产工艺的要求,就可以说是一种好的的设计。但为了满足电气控制设备的制造和使用要求,必须进行合理的电气控制工艺设计。这些设计包括电气控制柜的结构设计、电气控制柜总体配置图、总接线图设计及各部分的电器装配图与接线图设计,同时还要有部分的元件目录、进出线号及主要材料清单等技术资料。
2、电气控制柜总体配置设计
电气控制柜总体配置设计任务是根据电气原理图的工作原理与控制要求,先将控制系统划分为几个组成部分(这些组成部分均称作部件),再根据电气控制柜的复杂程度,把每一部件划成若干组件,然后再根据电气原理图的接线关系整理出各部分的进出线号,并调整它们之间的连接方式。总体配置设计是以电气系统的总装配图与总接线图形式来表达的,图中应以示意形式反映出各部分主要组件的位置及各部分接线关系、走线方式及使用的行线槽、管线等。
电气控制柜总装配图、接线图(根据需要可以分开,也可并在一起)是进行分部设计和协调各部分组成为一个完整系统的依据。总体设计要使整个电气控制系统集中、紧凑,同时在空间允许条件下,把发热元件,噪声振动大的电气部件,尽量放在离其它元件较远的地方或隔离起来;对于多工位的大型设备,还应考虑两地操作的方便性;控制柜的总电源开关、紧急停止控制开关应安放在方便而明显的位置。总体配置设计得合理与否关系到电气控制系统的制造、装配质量,更将影响到电气控制系统性能的实现及其工作的可靠性、操作、调试、维护等工作的方便及质量。
2.1电气控制柜组件的划分
由于各种电器元件安装位置不同,在构成一个完整的电气控制系统时,就必须划分组件。划分组件的原则是:
(1)把功能类似的元件组合在一起;
(2)尽可能减少组件之间的连线数量,同时把接线关系密切的控制电器置于同一组件中;
(3)让强弱电控制器分离,以减少干扰;
(4)为力求整齐美观,可把外形尺寸、重量相近的电器组合在一起;
(5)为了电气控制系统便于检查与调试,把需经常调节、维护和易损元件组合在一起。
2.2在划分电气控制柜组件的同时要解决组件之间、电气箱之间以及电气箱与被控制装置之间的连线方式:电气控制柜各部分及组件之间的接线方式一般应遵循以下原则:
(1)开关电器、控制板的进出线一般采用接线端头或接线鼻子连接,这可按电流大小及进出线数选用不同规格的接线端头或接线鼻子;
(2)电气柜、控制柜、柜(台)之间以及它们与被控制设备之间,采用接线端子排或工业联接器连接;
(3)弱电控制组件、印制电路板组件之间应采用各种类型的标准接插件连接;
(4)电气柜、控制柜、柜(台)内的元件之间的连接,可以借用元件本身的接线端子直接连接,过渡连接线应采用端子排过渡连接,端头应采用相应规格的接线端子处理。
3、电器元件布置图的设计与绘制
电气元件布置图是某些电器元件按一定原则的组合。电器元件布置图的设计依据是部件原理图、组件的划分情况等。设计时应遵循以下原则:
(1)同一组件中电器元件的布置应注意将体积大和较重的电器元件安装在电器板的下面,而发热元件应安装在电气控制柜的上部或后部,但热继电器宜放在其下部,因为热继电器的出线端直接与电动机相连便于出线,而其进线端与接触器直接相连接,便于接线并使走线最短,且宜于散热;
(2)强电弱电分开并注意屏蔽,防止外界干扰;
(3)需要经常维护、检修、调整的电器元件安装位置不宜过高或过低,人力操作开关及需经常监视的仪表的安装位置应符合人体工程学原理;
(4)电器元件的布置应考虑安全间隙,并做到整齐、美观、对称,外形尺寸与结构类似的电器可安放在一起,以利加工、安装和配线。若采用行线槽配线方式,应适当加大各排电器间距,以利布线和维护;
(5)各电器元件的位置确定以后,便可绘制电器布置图。电气布置图是根据电器元件的外形轮廓绘制的,即以其轴线为准,标出各元件的间距尺寸。每个电器元件的安装尺寸及其公差范围,应按产品说明书的标准标注,以保证安装板的加工质量和各电器的顺利安装。大型电气柜中的电器元件,宜安装在两个安装横梁之间,这样,可减轻柜体重量,节约材料,另外便于安装,所以设计时应计算纵向安装尺寸;
(6)在电器布置图设计中,还要根据本部件进出线的数量、采用导线规格及出线位置等,选择进出线方式及接线端子排、连接器或接插件,并按一定顺序标上进出线的接线号。
4、电器部件接线图的绘制
电气部件接线图是根据部件电气原理及电器元件布置图绘制的,它表示成套装置的连接关系,是电气安装、维修、查线的依据。接线图应按以下原则绘制:
(1)接线图相接线表的绘制应符合GB6988.6-1993中《控制系统功能表图的绘制》的规定;
(2)所有电气元件及其引线应标注与电气原理图中相一致的文字符号及接线号。原理图中的项目代号、端子号及导线号的编制分别应符合GB5094-1985《电气技术中的项目代号》、GB4026-1992《电器设备接线端子和特定导线线端的识别及应用字母数字系统的通则》及GB4884-1985《绝缘导线标记》等规定;
(3)与电气原理图不同,在接线图中同一电器元件的各个部分(触头、线圈等)必须画在一起;
(4)电气接线图一律采用细线条绘制。走线方式分板前走线及板后走线两种,一般采用板前走线,对于简单电气控制部件,电器元件数量较少,接线关系又不复杂的,可直接画出元件间的连线;对于复杂部件,电器元件数量多,接线较复杂的情况,一般是采用走线槽,只要在各电器元件上标出接线号,不必画出各元件间连线;
(5)接线图中应标出配线用的各种导线的型号、规格、截面积及颜色要求等;
(6)部件与外电路连接时,大截面导线进出线宜采用连接器连接,其它应经接线端于排连接。
5、电气控制柜及非标准零件图的设计
电气控制装置通常都需要制作单独的电气控制柜、箱,其设计需要考虑以下几方面:
(1)根据操作需要及控制面板、箱、柜内各种电气部件的尺寸确定电气箱、柜的总体尺寸及结构型式,非特殊情况下,应使电气控制柜总体尺寸符合结构基本尺寸与系列;
(2)根据电气控制柜总体尺寸及结构型式、安装尺寸,设计箱内安装支架,并标出安装孔、安装螺栓及接地螺栓尺寸,同时注明配作方式。柜、箱的材料一般应选用柜、箱用专用型材;
(3)根据现场安装位置、操作、维修方便等要求,设计电气控制柜的开门方式及型式;
(4)为利于控制柜箱内电器的通风散热,在箱体适当部位设计通风孔或通风槽,必要时应在柜体上部设计强迫通风装置与通风孔;
(5)为便于电气控制柜的运输,应设计合适的起吊勾或在箱体底部设计活动轮。
总之,根据以上要求,应先勾画出电气控制柜箱体的外形草图,估算出各部分尺寸,然后按比例画出外形图,再从对称、美观、使用方便等方面进一步考虑调整各尺寸比例。电气控制柜外表确定以后,再按上述要求进行控制柜各部分的结构设计,绘制箱体总装图及各面门、控制面板、底板、安装支架、装饰条等零件图,并注明加工要求,再视需要为电气控制柜选用适当的门锁。当然,电气柜的造形结构各异,在柜体设计中应注意吸取各种型式的优点。对非标准的电器安装零件,应根据机械零件设计要求,绘制其零件图,凡配合尺寸应注明公差要求,并说明加工要求。
最后,还要根据各种图纸,对电气控制柜需要的各种零件及材料进行综合统计,按类别列出外购成品件的汇总清单表、标准件清单表、主要材料消耗定额表及辅助材料定额表等,以便采购人员、生产管理部门按设备制造需要备料,做好生产准备工作,也便于成本核算
三 : 气动系统的设计计算
气动系统的设计一般应包括:
1)回路设计;
2)元件、辅件选用;
3)管道选择设计;
4)系统压降验算;
5)空压机选用;
6)经济性与可靠性分析。
以上各项中,回路设计是一个“骨架”基础,本章着重予以说明,然后结合实例对气对系统的设计计算进行综合介绍。
1 气动回路
1.1 气动基本回路
气动基本回路是气动回路的基本组成部分,可分为:压力与力控制回路、方向控制(换向)回路、速度控制回路、位置控制回路和基本逻辑回路。表42.6-1 气动压力与力控制回路及特点说明
简图说明
1.压力控制回路
一次压控制回路
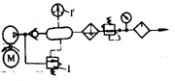
主要控制气罐,使其压力不超过规定压力。常采用外控式溢流阀1来控制,也可用带电触点的压力表1′,代替溢流阀1来控制压缩机电动机的启、停,从而使气罐内压力保持在规定压力范围内。采用溢流阀结构简单、工作可靠,但无功耗气量大;后者对电动机及其控制要求较高
二次压控制回路
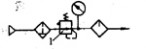
二次压控制主要控制气动控制系统的气源压力,其原理是利用溢流式减压阀1以实现定压控制
高低压控制回路
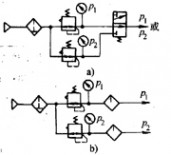
气源供给某一压力,经二个调压阀(减压阀)分别调到要求的压力
图a利用换向阀进行高、低压切换
图b同时分别输出高低压的情况
差压回路
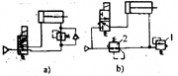
此回路适用于双作用缸单向受载荷的情况,可节省耗气量
图a为一般差压回路
图b在活塞杆回程时,排气通过溢流阀1,它与定压减压阀2相配合,控制气缸保持一定推力
2.力控制回路
串联气缸增力回路
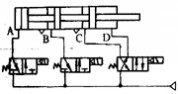
三段活塞缸串联。工作行程(杆推出)时,操纵电磁换向阀使活塞杆增力推出。复位时,右端的两位四通阀进气,把杆拉回
增力倍数与串联的缸段数成正比
气液增压缸增力回路

利用气液压缸1,把压力较低的气压变为压力较高的液压,以提高气液缸2的输出力。应注意活塞与缸筒间的密封,以防空气混入油中
1.1.1 压力与力控制回路(见表42.6-1)
1.1.2换向回路(见表42.6-2)
表42.6-2 气动换向回路及特点说明
简图说明
1.单作用气缸换向回路
二位三通电磁阀控制回路

图a为常断二位三通电磁阀控制回路。通电时活塞杆上升,断电时靠外力(如弹簧力等)返回
图b为常通二位三通电磁阀控制回路。断电时常通气流使活塞杆伸出,通电时靠外力返回
三位三通电磁阀控制回路
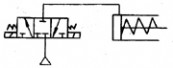
控制气缸的换向阀带有全封闭形中间位置,理论上可使气缸活塞在任意位置停止;但实际上由于漏损(即使微量)而降低了定位精度
此三位三通阀可用三位五通阀代替
二位三通阀代用回路
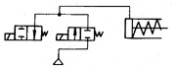
用两个二位二通电磁阀代替二位三通阀以控制单作用缸工作。图示位置为活塞杆缩回位置;需要活塞杆伸出时,必须两个二位二通阀同时通电换向
2.双作用气缸换向回路
二位五通单电(气)控阀控制回路
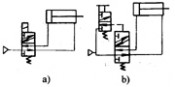
图a为单电磁控制阀控制回路。电磁阀通电时换向,使活塞杆伸出。断电时,阀芯靠弹簧复位,使活塞杆收回
图b为单气控换向阀控制回路。切换二位三通阀时相应切换主气控阀,使活塞杆伸出。二位三通阀复位后主气控阀也复位,活塞杆缩回
二位五通阀代用回路
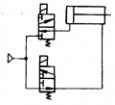
用两个二位三通电磁阀代替上述二位五通阀的控制回路中,两个阀一为常通,另一为常断,且两阀应同时动作,才能使活塞杆换向
二位五通双电(气)控阀控制回路
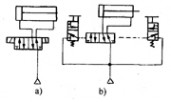
图a为双电控双作用缸换向回路
图b为双气控双作用缸换向回路。主控阀两则的两个二位三通阀可作远距离控制用,但两阀必须协调动作,不能同时接通气源
三位五通双电控阀控制回路
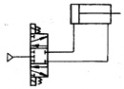
此回路除可控制双作用缸换向外,气缸可以在中间位置停留
1.1.3速度控制回路(见表42.6-3)
表42.6-3 气动速度控制回路及特点说明
简图说明
1.单作用缸速度控制回路
调速回路
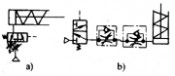
图a为采用节流阀的回路
图b为采用单向节流阀的回路。两单向节流阀分别控制活塞杆进退速度
快速返回回路

活塞返回时,气缸无活塞杆腔由于经快速排气阀直接排气,就使活塞杆快速返回
2.双作用气缸速度控制回路
调速回路
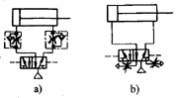
图a为采用单向节流阀的调速回路
图b为采用节流阀的调速回路
图a、b都是排气节流调速回路。对于气动,采用排气节流较进气节流效果好。因为,前者可使进气阻力小;且活塞在有背压情况下向前运动,运动较平稳,受外载变化的影响较小
缓冲回路
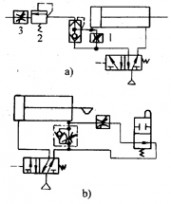
缓冲回路即为行程末端变速回路
图a当活塞返回到行程末端时,其左腔压力已下降到打不开溢流阀2,因此残气只能通过节流阀1缓冲排出,节流阀3开度较大,不影响末端行程前的正常排气。它常用于行程长、速度快的场合
图b当活塞杆伸出至撞块切换二通阀时开始缓冲。根据缓冲要求,可改变二通阀的安装位置,达到良好的缓冲效果。此回路适用于气缸惯性力大的场合
3.气液联动速度控制回路
气液传送器调速回路
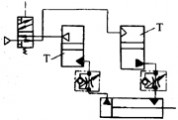
此回路通过改变油路中节流开度来达到两个运动方向的无级调速。它要求气液传送器T的油量大于液压缸的容积,并有一定余量,同时须注意气、油间的密封、以防气体混入油中
变速回路(快进-慢进-快退)
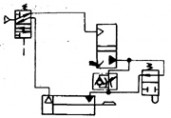
当活塞杆伸出至撞块切换二通行程阀后,活塞运动开始从快进变为慢进。改变单向节流阀节流开度,可获任意低速
气液传动缸调速回路
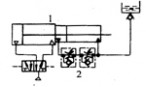
该回路通过调节两只速度控制阀2的节流开度来分别获得二个运动方向的无级调速。油杯3起补充漏油的作用
图中1为气液传动缸
变速回路之一(快进-慢进-快退)
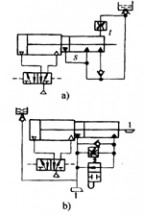
图a回路为液压缸结构变速回路:当活塞右行至封住s孔开始,液压缸右腔油液只能被迫从t孔经节流阀至其左腔,这时快进变为慢进。此回路变速位置不能改变
图b回路为用行程阀变速的回路:当活塞右行至撞块1碰到行程阀后开始作慢速进给。此回路只要改变撞块安装位置即可改变开始变速的位置
变速回路之二(快进-慢进-慢退-快退)
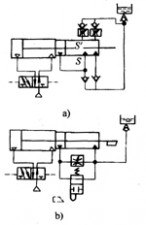
图a回路为液压缸结构变速回路:当活塞右行至超过s孔时,开始从快进变为慢进。而当活塞左行时,由于其左腔油液只能被迫从s′孔经节流阀至其右腔,故为慢退,直至活塞左行到超过s孔时,才开始从慢退变为快退
图b回路为采用行程阀的回路。慢退的实现是由于它比采用行程阀的快进→慢进→快退回路少了一只单向阀,活塞开始左行时其左腔的油液只能经节流阀流至其右腔
变速回路之三(中间位置停止)
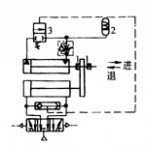
回路中,阻尼缸与气缸并联,液压缸流量由单向节流阀来控制,可得平稳而一定的速度。弹簧式蓄能器2能调节阻尼缸中油量变化,且有补偿少量漏油作用。借助阻尼缸活塞杆上的调节螺母1,可使气缸开始时快速动作,当碰到螺母后,就由阻尼缸来控制,变为慢速前进。同时,由于主控阀采用了中间泄压式三位五通阀,所以当主控阀在中间位置时,油阻尼缸回路被二位二通阀3切断,活塞就停止在该位置上;当主阀被切换到任何一侧,压缩空气就输入气缸,同时经梭阀使阀3换向,使液压回路接通阻尼缸起调速作用。并联活塞杆工作时由于产生附加弯矩,故应考虑设导向装置
1.1.4 位置控制回路(见表42.6-4)
表42.6-4 气动位置控制回路及特点说明
简图说明
1.有限(选定)位置控制回路
缓冲挡块
定位控制
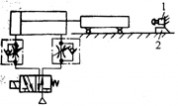
当执行元件(如气缸活塞杆)把工件推到缓冲器1上时,使活塞杆缓冲行进一小段后,小车碰到定位块上,使小车强迫停止
气控机械
定位机构
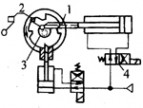
水平缸活塞杆前端联接齿轮齿条机构。当活塞杆及其上齿条1往复动作时,推动齿轮3往复摆动以带动齿轮上棘爪摆动,推动棘轮作单向间歇转动,从而带动与棘轮同轴的工作转台作间歇转动。工作台下带有凹槽缸口,当水平缸活塞杆回程时,即齿条脱开行程开关2时,使垂直缸电磁阀4切换,垂直缸活塞杆伸出,进入该凹槽缺口,使工作转台正确定位
多位缸位置控制
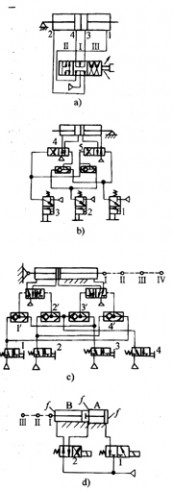
多位缸位置控制回路的特点是控制多位缸的活塞杆按设计要求,部分或全部伸出或缩回,以获得多个位置
图a利用三位六通阀的回路:当阀处于位置I时,气缸处于图示位置(两端活塞杆处于收缩状态);阀处于位置Ⅱ时,孔2、3进气,右活塞杆伸出;阀处于位置Ⅲ时,两端活塞杆全部伸出
图b由二位三通阀1、2、3控制两个换向阀4、5,使气缸两活塞杆处于所要求位置:阀1动作时,两活塞杆均收进;阀2动作时,两杆一伸一缩;阀3动作时,两杆全部伸出
图c四位置定位控制回路。图示位置为按动手控阀1时,压缩空气通过手控阀1,分两路分别由梭阀1′、4′控制两个二位五通阀使主气源进入多位缸而得到位置I。当推动手控阀2、3或4时,可相应得到位置Ⅱ、Ⅲ或Ⅳ
图d为A、B两缸串列实现三位定位控制的回路。图示位置为A、B两缸的活塞杆均处于收进状态。当左阀2如图示状态而右阀1通电换向时,由于A缸活塞面积较B缸为大,故A缸活塞杆向左推动B缸活塞杆,其行程长为Ⅰ-Ⅱ。反之,当阀1如图示状态而阀2通电切换时,缸B活塞杆杆端由位置Ⅱ继续前进到Ⅲ(因缸B行程长为Ⅰ-Ⅲ)。此外,可在两缸端盖上?处与活塞杆平行安装调节螺钉,可微调行程位置
1.有限选定控制回路
多位缸位置控制
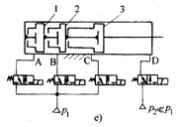
图e不三柱塞数字缸位置控制回路。A、B、C、D为气缸的四个通口:A、B、C供正常工作压力p1,通口D供低压,以控制各柱塞复位或停于某个需要位置。1、2、3为三个柱塞。当控制不同换向阀工作时,可得到包括原始位置在内的活塞杆的八个位置:1、2、3三个柱塞各自分别伸出时可相应得到三个不同位置;1、2同时伸出,2、3同时伸出或1、3同时伸出时又可得三个不同位置;1、2、3全部伸出为此数字缸最大行程位置;1、2、3均收进为图示原始位置
2.任意位置停止控制回路
三位阀位置控制回路 用三位三通阀或三位、五通阀控制普通气缸位置(参阅表42.6-2中的有关回路) 三位三通阀控制普通单作用气缸,三位五通阀控制普通双作用气缸
这类位置控制回路由于要求气动系统,主要是缸与阀元件的密封性很严,否则不易正确控制位置,对于要求保持一定时间的中停位置更为困难。所以这类回路可用于不严格要求位置精度的场合
气液联动控制位置回路
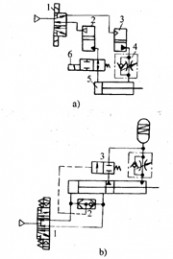
图a由于采用了气液传送器2、3,所以与上述普通气缸的位置控制回路的精度要高得多。缸的活塞杆伸出端装有单向节流阀4以控制回程速度;缸的另一端装有两位两通换向阀6,需要在中间位置停止时,将液压回路切断,迅速地使活塞停留在所要求的位置上
图b为采用气液阻尼缸的气液联动位置控制回路。换向阀1为中泄式三位五通阀。图示位置时,气液缸的气缸部分排空;而液压缸部分由于两位两通阀3处于封闭位置,回路断开,故可保持活塞杆停在该位置。当阀1切换时,由于压缩空气除进入气缸外,还可经梭阀2而切换阀3,使气液阻尼缸的阻尼油路通,即可由气缸推动液压缸工作
1.1.5 基本逻辑回路(见表42.6-5)表42.6-5 气动基本逻辑回路及特点说明
简图说明
逻辑符号及表示式真值表、其他信号动作关系
是回路


as
00
11
非回路


as
01
10
或回路

abs
000
011
101
111
与回路

abs
000
010
100
111
或非回路
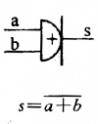
abs
001
010
100
110
与非回路

abs
001
011
101
110
禁回路
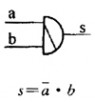
abs
000
011
100
110
独或回路
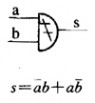
abs
000
011
101
110
同或回路
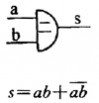
abs
001
010
100
111
记忆回路
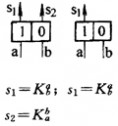
abs1s2
1010
0010
0101
0001
延时回路

当有控制信号a时,需经一定时间延迟后才有输出s
延时τ的长短可由节流元件调节。回路要求信号a的持续时间大于τ
脉冲信号
形成回路

回路可把一长信号a变为一定宽度的脉冲信号s,脉冲宽度可由回路中节流元件进行调节
回路要求输入信号a的持续时间大于脉冲宽度
1.2 常用回路
实际应用中经常遇到的典型回路简称常用回路。
1.2.1 安全保护回路(见表42.6-6)
1.2.2往复动作回路(见表42.6-7、8)表42.6-6 气动安全保护回路及特点说明
简图说明
1.过载保护回路
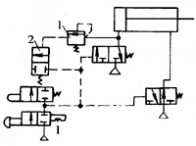
气缸活塞在右行途中,若遇障碍或其它原因而使气缸过载时,气缸左腔压力急剧升高,当超过预定值时,顺序阀1打开,二通阀2打开,主控阀控制气由阀2排空而复位,从而使气缸左腔排气,活塞杆收回。因此本回路实质为限压回路
2.互锁及供气选择回路
互锁回路
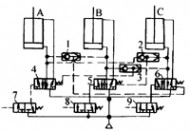
互锁回路可保证同时只有一个缸动作。回路主要利用梭阀1、2、3及换向阀4、5、6进行互锁。如气控阀7动作,换向阀4换向使A缸动作;但同时缸A进气腔管路使梭阀1、2动作,把换向阀5、6锁住;这样,此时即使有气控阀8、9的动作信号,B、C缸也不会动作。如需换缸动作,必须把前面动作缸的气控阀复位才行。
供气选择回路
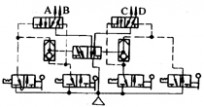
此回路为四个空气供应站A、B、C、D的选择回路:同时只允许有一个站供气(输出)。其动作原理与上述互锁回路相似
3.双手“同时”操作回路

此回路为需双手“同时”操作才能使活塞运动的回路。若双手不是“同时”按下,则气容3都将首先与阀1的排气口接通而排空,使无K信号。若阀1或2未能复位,则气容3都将得不到充气,亦就不可能有K气信号。故此回路能确保手的安全
表42.6-7 气动往复动作回路及特点说明
简图说明
1.单往复动作回路
行程阀控制回路
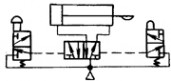
这是利用右端行程阀控制的单(一次)往复动作回路。其结构较简单、操作方便(按一下左端按钮阀,气缸活塞进行一次往复动作)
延时返回回路
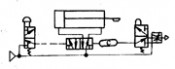
此回路与上述回路比较多了一个气容c。活塞右行达到所定行程,压下行程阀后,气源对c充气后主控阀才换向,使活塞返回
2.连续往复动作回路
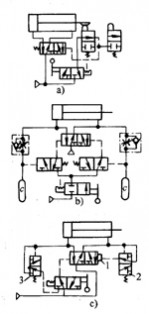
图a为较简单的利用行程阀实现连续自动往复的回路,其可靠性常取决于行程阀的密封性与弹簧的质量
图b为时间控制式回路。利用气容元件c充气达一定值时切换主控阀,从而实现活塞行程连续自动往复。回路较a复杂,但是可不用行程阀,且外接管路也较少
图c为压力控制式回路。它适用于行程短、不便安装行程阀的场合。当载荷变化较大时,为使缸正常工作,应使缸径选择有较大余量。当要求行程位置较准确时,主控阀应选为差压阀(如图c中之1),两侧两个阀2、3也要选择合适
表42.6-8 气动程序动作控制回路举例及特点说明
简图说明
A1-B1-B0-A0双缸程序动作回路
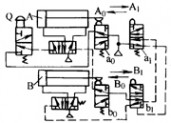
两缸A、B按A1-B1-B0-A0程序进行工作
回路中行程阀b1为气控复位式的,它与a1、b0采用可通过式行程阀的回路比较,能在速度较快的情况下正常工作
图中Q为起动阀。当按下Q阀时,缸A的主控阀将气源与缸A左侧联通,使缸A处于A1状态,以下即按程序A1-B1-B0-A0工作
1.2.3程序动作控制回路
程序动作控制回路(表42.6-8)在实际中应用广、类型多。下面仅举一个双缸程序动作(A1-B1-B0-A0)为例(表42.6-8)说明。而不同执行缸以及各种不同程序动作的回路,将在本章第2节中介绍其基本设计方法。
1.2.4同步动作控制回路(见表42.6-9)表42.6-9 气动同步动作控制回路及特点说明
简图说明

1)为较简单的同步回路。使A、B两缸同步的主要措施是采用刚性零件G连接两缸的活塞杆
2)是通过把油封入回路中来达到两缸正确地同步的。由于两缸为单活塞杆缸故要求气液缸B的内径大于缸A的内径,以使气液缸B上腔的有效截面积与缸A的下腔截面积完全相等。若两缸为双活塞杆缸,则要求两缸内径与活塞杆直径均相等
3)是使加有不等载荷F1、F2的工作台作水平上下运动的同步动作回路。当三位主控阀处于中间位置时,蓄能器自动地通过补给回路对缸补充漏油。若主控阀处于另两位置,则蓄能器的补给回路被切断,回路中还安装了空气塞1、2,可将混入油中的空气放掉并由蓄能器补油
气动逻辑设计方法
浏览字体设置:- +

放入我的网络收藏夹
气动逻辑设计方法
本节主要介绍气动控制中应用较广的行程程控的回路设计方法。
气动行程程控回路设计方法可归纳为两大类:直观组合法与逻辑设计法。直观组合法就是利用前述的基本回路与常用回路,考虑起动、急停、复位、延时等要求,适当予以组合而成为符合某一要求的程控回路。这种设计方法适用于较简单的回路设计,并常需辅以必要的检验修正。对于较复杂或含有多往复动作的回路,则常需采用逻辑设计法。其中常用的有:信号动作状态线图法(简称X-D线图法)、逻辑运算法、卡诺图法、列表法(Q-M法)以及计算机辅助简化法(CAS法)等。这些方法都具有四个过程:行程程序输入、逻辑处理、逻辑原理图绘制与气控回路图绘制。各种方法的区别主要在于逻辑处理的方式方法,其次是行程程序输入也稍有不同。其中,X-D线图法较直观,但处理过程较繁;逻辑运算法比较抽象;卡诺图法较直观,且处理规则性较强。因此,当变量(取决于动作要求与变化情况)不大于8个时,用得较多,否则逻辑处理相当庞杂而困难。多变量的情况可采用Q-M法,但变量增多,列表也愈益繁难,这时可用CAS法来进行逻辑处理。下面主要介绍常用的X-D线图法与卡诺图法。
2.1 X-D线图设计法
内容与步骤:
1)绘工作行程顺序图。
2)缓X-D线图。
3)消除控制障碍、确定执行信号。
4)绘气控逻辑原理图。
5)绘气动回路原理图。
绘制X-D线图所使用的符号,除应符合GB/T7861-1993的规定外,特殊符号及其说明见表42.6-10。表42.6-10 X-D线圈所用规定符号说明
符号说明
A、B、C、…表示气缸A、B、C、…
a、b、c、…表示与气缸A、B、C、…相对应的行程阀及其发出的信号a、b、c、…
A0、A1表示气缸A的两个不同动作状态,带下标“0”为气缸缩回状态,下标“1”为伸出状态
a0、a1表示与气缸A0、A1相对应的不同动作状态的行程阀。a0为对应于缸收回位置的行程阀,a1为对应于缸伸出位置的行程阀
在X-D图上,还可表示与缸动作状态相对应的工作输出信号
a0*、a1*、b0*、b1*…a0*、b0*、…在X-D图上,右上角带“*”号的信号称为执行信号(如a0*),不带*的信号(如a0)称为原始信号。原始信号是指来自发信器(如行程阀)的信号,它分有障(碍)与无障两种。但执行信号必为无障信号,所以执行信号可以是无障信号或是有障原始信号,但已经过逻辑处理而排除了障碍的信号
a1*= a1执行信号a1*就是原始无障信号a1
a1*= b1·a1a1为原始有障信号时,则其执行信号a1*必须把障碍排除后,如用逻辑“与”消障,即b1、a1
→表示“控制”,如a0→B1表示a0(行程阀a0工作输出信号)控制B缸伸出动作

粗实线表示气缸的动作状态线,细实线为控制信号状态线;“○”—起始,“×”—终了,

—起始终了时间很短的脉冲信号
——— ﹋﹋信号线下的波浪线段表示该段信号使执行元件进退两难,即为有障碍信号段
----粗虚线表示“多往复”系统中重复动作状态的补齐线;细虚线表示重复信号补齐线
2.1.1 双控主控阀控制回路的设计
(1)绘工作行程顺序图
对生产对象,经过调查研究,明确所控制执行元件的数目、动作顺序关系以及其他控制要求(如手动、自动控制等),列出工作行程程序。
具体方法是:每个执行元件都有其各自的号码(如缸A、B、…);每个执行元件的每个动作都作为一个工作程序写出来(如A0、A1、…);程序之间,即每个动作的工作状态之间用带“控制箭头→”的连线连接,箭头指向即表示动作程序进行的方向,箭头线上对应于执行元件的行程阀输出信号用小写字母表示(如a0、a1、…)。
例1画出某专用气动机械手(图42.6-1)的工作行程顺序图。其动作程序图和工作顺序图分别为图42.6-1b和图42.6-1c。
该机械手的执行元件(缸或马达)数为4。正、反转,下降、上升,伸出、缩回,夹紧、松开的相应编号为:A1、A0、B0、B1、D1、D0、C1、C0。两个相邻程序动作之间加上相应的行程阀输出信号,如状态A1之后加上行程阀a1,D1之后加上d1等。并且,在每一动作状态下标上程序号。画出工作行顺序图,见图42.6-1c。程序中:“→”指向表示控制顺序的方向,如

表示b0控制D缸伸出动作。
(2)绘制信号-动作状态线图(X-D线图)
1)画方格图>根据例1列出的工作程序数及顺序,由左至右画方格并填上动作状态程序(D程序)序号1、2、…及相应的动作状态,如图42.6-2上面第一大横格所示,在最右边留一栏作为“执行信号栏”。在纵列最左边的宽纵格为控制信号及其控制的动作状态组(X→D组简称“组”)的序号及其相应的X→D组。每一X→D组包括上下两部分:上面为控制该动作状态的行程信号状态,如c0(A1)、a1(B0)、…;下面为该信号控制的动作状态,如A1、B0、…。c0(A1)表示控制A1动作的信号c0,a1(B0)表示控制B0动作的信号a1。最下一行是为消除障碍找出执行信号进行逻辑运算的备用格。
图42.6-2所示为例1专用气动机械手回路设计过程中采用X/D线法绘制的X/D线图的方格图。
2)画动作状态线>用横粗实线把所有动作状态线画出。图42.6-3为例1气动机械手X-D线图的动作状态线图。
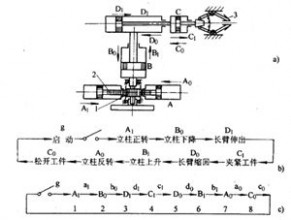
图42.6-1 气动机械手
a)气动机械手示意图;b)动作程序图;c)工作顺序图
A—立柱回转缸;B—立柱升降缸;C—夹紧缸;D—长臂伸缩缸
1—齿轮;2—齿条;3—手爪
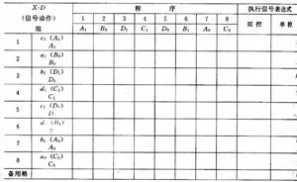
图42.6-2 气动机械手X-D线图的方格图
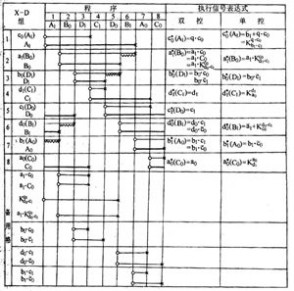
图42.6-3 气动机械手X-D线图
动作状态线的开始与终止点画法规律如下:
①起点,必然是该动作状态程序开始处。如D1(D缸伸出)位于第3组、第3程序,所以D1的动作状态线开始处必在第3程序开始处(左端)。
②终点,必然是该动作状态变换开始处。如D缸伸出状态D1变换为D缸缩回状态D0。所以状态线的终点必在D0开始处(稍前),位于第5组、第5程序,所以D1动作状态线的终点应在第5程序开始(左端)稍前处。因此D1的动作状态线应从第3程序画到第5程序开始前为止。同理,D0的状态线应从第5程序开始画到D1开始前的第3程序为止。
3)画信号状态线(简称信号线)见图42.6-3,用横细实线表示信号线,画在该信号所控制动作的状态线上方(同一格内)。
信号线的起点与终止点的画法规律如下:
起点,显然与此信号所控制缸的动作开始点相同。如信号c0控制A缸伸出动作A1,则c0的起点与A1相同。
终点,应与控制或产生此信号的缸的动作状态变换(如控制或产生信号c0的缸动作状态C0变换为c1)的开始点相一致。因此c0(A1)的信号由A1(第1组1程序)左端开始到C1(第4程序)左端开始点为止。
画信号线要注意以下问题:
如果信号起、终点在同一条纵向分界线上而出现“

”图线时,即表示该信号为脉冲信号。在气动回路中,该脉冲信号的宽度相当于行程阀发信、气控阀换向、气缸启动以及信号传输等时间的总和。
对于多缸多往复系统情况(在一个工作循环中,执行元件要作多次往复动作),必须注意由于“多往复”动作带来的多次动作状态与对应的信号各次互相间应该用虚线补齐不漏。这种系统的特点及由此决定的画法(补线)简述如下:
①由于同一行程信号(在不同程序组)重复发出以控制不同对象(如b0→B1,b0→A0)或同一对象的不同动作状态。这样,重复信号(如b0)的每一次发出信号必然对控制两种状态(如B1、A0)的主控阀都起作用;因此,应在重复信号(如两次b0)的相应信号线上相互对应用虚线补齐,见图42.6-4中第4组与第6组中的i-i′以及h-h′。
②由于同一动作的多次往复,某些主控阀及其相应执行元件可能受不同信号所控制,如B1在第2程序受信号a1控制而在第4程序中则受信号b0控制;这就必然增多了动作状态线。又见图42.6-4中的第3、5组之间重复动作B0,相应地补上了0′与p′两条虚线以表示重复动作状态B0的补齐线。
对于“多往复”系统的动作关态线和信号线画法举例说明如下。例2 有一双缸“多往复”系统,其动作程序为
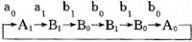
,其相应的X-D图如图42.6-4所示。图中实线表示按“单往复”情况下动作状态线及相应的信号线;而虚线则表示“多往复”情况所增多的动作状态线及相应的控制信号线。
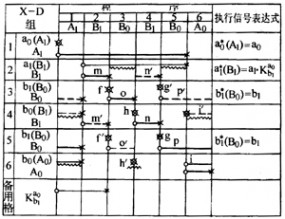
图42.6-4 双缸“多往复”回路X-D图图例
增多线的补齐应使动作与信号的相互关系如实反映,以便采取措施以保证协调动作。所以,首先应分析清楚“多往复”的动作与信号哪些是重复的,在什么组、什么程序范围内重复,如例2所示动作状态线B1在第2程序与第4程序重复,B0在第3和第5程序重复;而相应的信号b1在第3组以及第5组时、b0在第4组以及第6组时重复作用。
补齐重复动作状态线的要点为:把重复的动作状态当作普通(非“多往复”)情况画上(如B1在第2组的第2程序、第4组的第4程序处都分别用粗实线画上m段与n 段,见图42.6-4);然后补上对应于相同程序而在不同组的动作线(如与B1在第2组第2程序m段相应的第4组第2程序的m′段;同理,对应于n段补上n′段)。同理,对于动作状态B0的重复状态线:先画上o、p段,然后补上相应的o′、p′段。
补齐重复信号线的要点与补齐动作状态线的基本相同,但补齐信号线且虚细线来表示,如图42.6-4中所示。对于信号b1;在第2程序对应于第3组的脉冲信号f,在第5组补上相应的脉冲信号f′;在第5程序对应于第5组的脉冲信号g,在第3组补上相应的脉冲信号g′。同理,对于信号b0:在第4程序对应于h补上h′;在第6程序到下一循环的第1程序范围内对应于第6组的信号线i;在第4组补上相应信号线i′。
对于X-D线图,在画出全部动作状态线及信号线后,还必须分析动作与信号之间是否协调。如果动作与信号协调,即不存在障碍,则可把X-D线图上各组中控制信号定为执行信号,并据此画出逻辑原理图与回路设计图。如果存在障碍,则必须采取排除障碍的措施,把有障原始信号变为已排除了障碍的执行信号,然后也可据此画出逻辑原理图与回路设计图。
(3)消除障碍与确定执行信号
1)障碍类型—I型、Ⅱ型在X-D线图上的每一组中,都反映出某控制信号及其所控制执行元件(气缸或气马达)的动作状态。信号与动作状态的节拍(时间与程位)必须按程序要求正确配合:控制信号必须满足程序动作状态的变换要求(正动、逆动、停止等)。如果动作状态要变换而控制信号不允许其变换,系统即出现故障。障碍动作状态变换的控制信号称为障碍信号。障碍信号延续的长度称为障碍段,它在X-D线图上用波浪线来表示,即在原来有障碍信号的细线下画上波浪线,见图42.6-3。
对于气缸控制系统,一般不要求其具有任意位置中停的性能。这时,障碍信号常表现为:在同一组中控制信号线的长度大于所控制的动作状态线的长度,其超出长度即为障碍段。多缸单往复系统所产生的障碍称为I型障碍,如图42.6-3中所示:a1(B0)、b0(D1)、d0(B1)和b1(A0)各信号的障碍信号均为I型障碍信号。多缸多往复系统由于多次重复信号所造成的障碍称为Ⅱ型障碍,如图42.6-4中所示。
对于气马达控制系统,通常要求其具有任意位置中停的性能。这是由于气马达的结构与工作原理特点所决定的。气缸只有活塞伸出和缩回两种工作状态,故选两位换向阀做主控阀就可满足要求。气马达则有正转、反转及中停三种动作状态,因此必须选用三位换向阀作主控阀。两位阀有记忆功能,故脉冲信号可用作控制信号,且无障碍;而三位阀无记忆功能,故脉冲短信号要求用作控制信号时,必须设法使其与受控的动作同步,在X/D线图上即表示为信号线要求与动作线拉成等长,否则将出现动作失控的情况。气控系统中信号线短于动作线的情况,虽然不能称作“障碍”,但也是必须在系统设计过程中,确定执行信号前,予以解决。
2)障碍信号的排除方法>对于I、Ⅱ型障碍,由于障碍信号段就是控制信号线多于(或长于)其所控制动作状态线的部分,实际上也就是控制信号的存在时间长于其所控制的动作状态存在时间;所以,常用的障碍信号排除方法实质上就在于缩短控制信号存在时间(使之短于或等于该信号所控制的动作状态时间);反映在回路设计过程的X/D线图上就是缩短控制信号线长度,使短于(或极限情况等于)此信号所控制的动作状态线的长度。常用的I型障碍与Ⅱ型障碍排除方法分别见表42.6-11、12。例1中相应的气控回路设计X/D线图(图42.6-3)中,信号线下画有波浪线的为障碍段,其右的执行信号即为障碍已被排除的信号。对于气动控制系统中,信号线长度短于动作状态线长度的失控情况,其解决方法一般是先用中间记忆元件(如记忆阀)将脉冲信号拉长(例如

x为脉冲短信号借助记忆阀K而拉长),然后再用逻辑“与”运算使执行信号线成为与动作状态线等长的正确信号。表42.6-11 I型障碍排除法(缩短控制信号障碍段排障法)
原理措施备注
逻辑运算(常为与)法排障系统中有直接可用作X的信号时
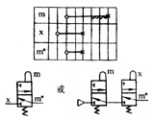
x的开始点应选在障碍信号m开始之前或同时(包括m障碍段之后)
x的终止点应选在障碍m的无障段
x尽量选用系统中某原始信号或主控阀输出信号 m—待排障的障碍信号:

S—为无障碍段
2—为障碍段
x—制约信号,即用以排除障碍的辅助信号
m*—执行信号
系统中无直接可用作制约信号的信号时逻辑式:
m*=m·

逻辑原理图:
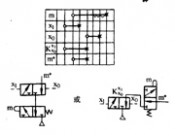

—常为双气控两位(三、四
通)阀;x1有气时,K阀有输出,和m相与得m*;x0有气时,K阀无输出。因此,K阀信号状态线应自x1的起点到x0的起点的连线
x1—K阀“通”信号,其起点应选在m的无障段之前或与m同时开始,其终点应选在m的无障段
x0—K阀“断”信号,其起点应选在m的起点之后,而到障碍段开始之前;其终点应选在x1起点之前,并且应使x0的终端长于x1的终端

—为一中间记忆元件
,由于系统中无可用作和m相“与”的制约信号,故另加一个辅助阀。以便和m相“与”排障后得m*
x1、x0—为阀K的两个控制信号
脉冲信号法排障机械方法活络挡块 活塞杆伸出时,活络挡块压行程阀发出脉冲信号(见图a);活塞杆收回时,活络块转上而通过行程阀,不发信号(图b)

机械法排障可简化回路,节省气动元件及管路
但不能用行程阀限位,只能用机械挡块或凸轮块大致控制气缸行程,这是因为用左图方法时,不可把行程阀安装在行程的末端,而必须留一段行程,以便挡块或凸轮能通过行程阀
通过式行程阀 活塞杆伸出时,杆端凸轮块压行程阀而发出脉冲信号(图a);活塞杆收回时,行程阀不发信号(图b)
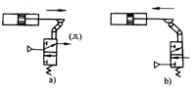
机械法排障可简化回路,节省气动元件及管路
但不能用行程阀限位,只能用机械挡块或凸轮块大致控制气缸行程,这是因为用左图方法时,不可把行程阀安装在行程的末端,而必须留一段行程,以便挡块或凸轮能通过行程阀
采
用
脉
冲
阀使用脉冲阀把长信号变为短信号
右图a为行程阀“与”脉冲阀气动回路
右图b为行程阀“与”差压控制脉冲阀气动回路右图c为图a情况加“启动保护”的回路

回路简单,但要注意调节好脉冲阀
必须注意检查回路在气源刚接通时是否有假脉冲信号(即不必要的信号),以免产生误动作。通常系统启动时如果脉冲行程阀被压,而输出的脉冲信号不是设计要求的,这时需加启动保护,即在输出阀控制端加延时回路,使假脉冲在启动时不产生障碍(如图c)
表42.6-12 Ⅱ型障碍排除法(信号分配法)
原理措施备注
某一多次重复信号先后控制各往复不同状态 系统中重复动作缸在两次往复之间存在独立中间信号采用中间记忆元件和双与门分配重复信号
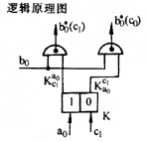
逻辑式
第一次b0产生b0*= b0·

第二次b0产生b0*= b0·

多次往复动作时,借助中间记忆元件(即两位双气控双稳阀K)及双与门,进行逻辑运算后(见上逻辑式),即进行信号分配,从而实现同一信号可先后控制不同状态工作
例如行程程序

中,B缸有两次往复重复动作B1B0……B1B0(一个工作循环中),其中同一b0信号先后分别控制不同动作状态C1,C0,故需引入中间记忆元件

并利用双与门:b0*(C1)= b0

b0*(C0)= b0·

即得到b0先后控制
C1与C0两种状态

双气控阀K的控制信号选取法:a0、c1必须是b0的两次重复信号间隔内独立出现(即无重复)的信号,如左例中两次b0重复信号的两次间隔内的c1及a0(或a1)信号,而且b1则不行,因有重复,会产生误动作;a0、c1应为短信号,否则仍会误动作
其操作控制程序为:
先输入置位信号a0,接着输入第一次b0相“与”得b0*得以控制C1;而后输入C1使K复位,则输入的第二次b0即为状态C0的控制信号 b0—有障碍的多次重复信号
b0*—经排障的执行信号
a0—记忆元件K的置“1”信号
c1—记忆元件K的置“0”信号
a0、c1不能同时存在,否则K阀不能正常工作。独立中间信号一两次b0信号之间独立出现的信号a0、c1、a1
系统中重复动作缸在多次往复之间没有独立的中间信号采用信号分配回路分配重复信号 控制二次往复的信号分配逻辑原理图
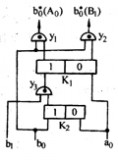
控制二次往复的信号分配回路图
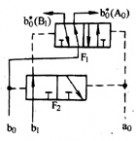
b0—有障碍的多次重复信号
b0*—信号分配后的执行信号
b1—连续往复中间信号
a0—置“0”信号
K1、K2—记忆元件(双稳)
F1、F2—分别为二位三通和二位五通阀
Y1、Y2、Y3—逻辑“与”元件
a0、b0—信号应为脉冲信号,以防有障碍
B缸两次重复动作:B1B0B1B0;例:

回路特点如下:
a0首先输入使K1、K2置“0”,当b1第1次输入后,Y3无输出,待b0第1次输入后,Y2有b0*(B1)输出,即控制了B1的动作。B0第1次输入另一作用使K1置“0”为下一次b0输入做准备。当b1第2次输入后使Y3输出,并切换K1置“1”,待b0第2次输入后Y1有b0*(A0)输出,控制了A1的动作 多次往复信号分配回路可采用一个共用的二位三通换向阀F2;而二位五通阀(或二位四通阀)F1,F2的数量为n,n=1+2(x-2),x为往复动作数目,x≥2(本例中B1B0B1B0两次往复x=2)n=1
不同信号控制同一多次缸状态
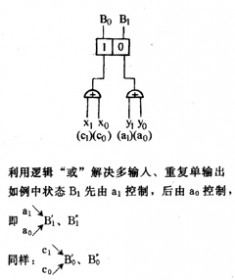
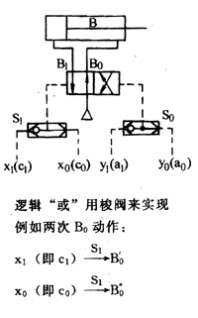
S—梭阀
x1、x0—控制同一重复状态的不同信号
y1、y0—控制另一重复状态的不同信号
B1、B0—B缸的两种状态

(4)绘制气控逻辑原理图
气控逻辑原理图是用气动逻辑符号来表示的控制原理图。
为了实现预定的程控动作要求,在X/D线图上用逻辑原理式表达的执行信号有待于发展为相应的控制原理图。也就是应该有一个由一定控制元件、并按照逻辑控制要求连接起来,再配以必要的其他回路要求(如手动、复位等)的回路控制原理图。因为由它可以方便地画出用阀类元件或逻辑元件组成的气控回路,以便对比选定较为合适的控制方式。
1)气控逻辑原理图的基本组成及其表示符号
①行程发信装置主要是行程阀,也包括外部输入信号装置,如启动阀、复位阀等。这些信号符号加以方框,如

…表示各种原始信号,而对其他手动阀及控钮阀等分别在方框上加相应的符号来表示,见图42.6-5左上部方框内标有q的框外符号即为手动启动阀。
②逻辑控制回路主要是“与”、“非”、“或”、“记忆”等逻辑功能,用相应符号来表示。注意这些符号应理解为逻辑运算符号,它不一定就代表一个确定的元件。因此,由逻辑原理图具体化为气动原理图时可有多种方案。例如“与”逻辑符号在逻辑元件控制时可为一种逻辑元件,而在气阀控制时可只表示一种串联连接。
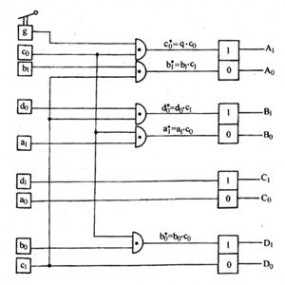
图42.6-5 气动机械手双控主控阀逻辑原理图图例
③执行机构的操纵阀,主要是主控阀,由于通常具有记忆能力,故常以记忆元件的逻辑符号

来表示;而执行机构,如气缸、气马达等,则通常只以其状态符号(如A0、A1)表示与主控阀相连 如

2)气控逻辑原理图的画法 根据X/D线图上执行信号栏的逻辑表达式,利用上述规定符号,按下列步骤画出:
①把系统中每个执行元件的两种状态分别与各自的主控阀相连后,自上而下一个个画在逻辑原理图的右边,如

②把发信器(如行程阀等)大致对应于其所控制的执行元件一个个列于逻辑原理图的最左边,见图42.6-5中左边的q、d0、…等。
③按执行信号的逻辑表达式,并考虑必要的操作要求增加的控制元件,如启动阀q等,把相关元件按逻辑关系连接,逐项画出逻辑原理图。
例1所示的气动机械手,其对应于信号状态线图(42.6-3)的气控逻辑原理图见图42.6-5。图中右边列出A、B、C、D四只气缸的八个动作状态及与其相连的四只主控阀。左侧列出全部行程阀,其上下次序无严格要求;但通常为减少画连接线时的交叉点,尽量使被控状态与相应信号放在相近行上。图的中段为控制段,要求正确地反映每个执行信号的逻辑关系:一是正确选用规定的逻辑符号,二是按逻辑式正确连接。至于启动信号阀q,由于只起回路启动作用,所以与第一程序c0*串联,即逻辑相“与”。
(5)绘制气动回路原理图
气动回路原理图是气控系统备件及安装调试的依据,也是绘制生产用施工图的基础(反映系统基本组成元件及其连接、工作原理)。下面介绍气动回路原理图的基本组成、连接关系及表示方法。
1)基本组成>与逻辑原理图相对应,气动回路原理图也有三个基本部分:
①执行元件及主控阀部分;
②各种行程发信装置,它可与执行元件(如气缸活塞杆)的被控位置相对应画出,也可集中画出(前者较直观,后者连接较清晰);
③控制部分,可根据具体情况而选用气阀元件、逻辑元件来实现。
通常把执行元件与主控阀用国家标准规定的图形符号画出,而对某些尚无明确规定符号的元件则可用习惯表示法来画。
此外,气动回路原理图根据需要还可包括:行程程序框图,气源压力控制和分配装置,与气控原理有关的速度控制、压力控制、时间控制等说明,与气控有关的电控回路图,标准件零件表以及非标准件、非通用件的必要技术资料(包括图纸)等。
2)回路连接>元件间连接的基本情况如下:
回路原理图的原始(静止)位置,一般规定为行程程序图上最后行程终了时刻的位置。因此,回路原理图上各元件(如气缸及其控制阀等)的状态及连接位置都是指在回路初始静止时的状态及连接位置。
①主控换向阀的气源应接在使活塞杆复位位置,即活塞杆原始静止位置(缩回或伸出),见图42.6-6a。位置是指主控阀常用四通(或五通)阀。
②行程阀及启动阀的连接,根据回路初始静止位置的不同可有:
阀处于工作状态(如行程阀被压上,见图42.6-6b):应使气源(包括直接与气源管道相接的有源阀以及与气源间接连接的无源阀两类)与输出通道在阀内连通,也就是使阀按“有输出”连接;并且应在靠近按钮的方块内表示出气源与输出连通的状况。
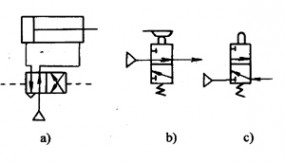
图42.6-6 回路中阀的连接
a)主控阀;b)工作状态行程阀;c)非工作状态行程阀
阀处于非工作状态:见图42.6-6c,应使阀按“无输出”状况连接(即气源与输出在阀内不连通),并且应在靠近复位弹簧的方块内表示。
③“与”、“或”、“非”、“记忆”等逻辑关系的联接,可按表42.6-5基本回路选取。相“与”的符号在回路上常用两个阀“串接”的方式,行程阀或启动阀常采用二位三通阀,有时需要“非”的信号也可用二位五通阀。
3)气动回路原理图的画法>气动回路原理图的表示方法常用的有以下三种,可根据具体情况选用:
①直观习惯画法(图42.6-7)其画法特点是:把系统中全部执行元件(如气缸、气马达等)水平或垂直排列,相应地在执行元件的下面或左侧画上对应的主控阀;而把行程阀较为直观地画在各气缸活塞杆伸、缩状态对应的水平位置上。图42.6-7即为对应于图42.6-5的气动回路图。
②仿逻辑原理图法(图42.6-8)其画法特点是执行元件、信号阀、控制部分的安排仿照逻辑原理图的安排。执行元件放在最右边,各缸自上至下平行排列,主控阀放在相应气缸的左下方:活塞杆伸缩两端点位置标注出相应行程阀的符号(如a0、a1、b0、b1等);但实际行程阀画在最左边;各阀接管位置是气源在左,输出口在右。
综上两种气动回路原理图的画法可以看出:直观习惯画法比较直观,但连接线规律性较差,且交叉点多;仿逻辑原理图法连接线交叉点较少,逻辑原理图画时较为方便,但直观性差。此外,如图42.6-7例中所示。行程阀应区别为:
有源行程阀(如例中a0、c0、c1等),与无源行程阀。有源行程阀的选用原则为:
1)一组或一个信号(行程阀)控制某一状态的情况,一组中应有一个为有源,单一的应为有源(包括相“或”的每个信号都应按单一信号算);
2)一组相“与”信号(行程阀串接)中,通常按程序最先出现的选用有源行程阀。
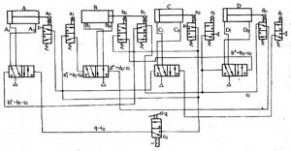
图42.6-7 双控主控阀直观习惯画法回路原理图
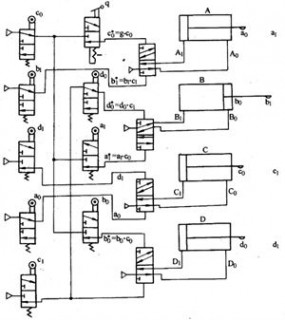
图42.6-8 气动机械手双控主控阀仿逻辑原理图画法气动回路图
2.1.2 单控主控阀控制回路的设计
气缸的往复动作采用单气(电)控主控阀(如弹簧复位阀)操纵,此类回路的主控阀只需一个执行信号控制,比双气控主控阀操纵的回路可省去复位阀及连接管路。若控制小直径的单作用气缸时,采用单控二位三通阀更为经济。
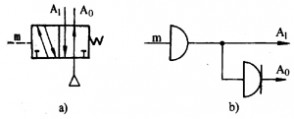
图42.6-9 单控两位阀的逻辑功能
(1)单控执行信号应满足的条件
由图42.6-9可知,单控二位五通阀从逻辑上讲,相当于一个“是门”和一个“非门”。

若已知主控阀如控制信号是m,输出信号是A1和A0,则m=A1=输出信号A1、A0,则单控执行信号m必满足m=A1。该条件在X-D线图上表现我为;单控执行信号的状态线必须和主控阀的输出状态等长。
(2)在X-D线图上确定执行信号的方法
下面以例1所示程序为例,说明确定单控执行信号的方法。
1)任何双控主控阀的一对执行信号,都可当作单控执行信号

的通、断信号t和d(虽然,单控执行信号是记忆信号,需注意:t·d=0)。如图42.6-3中的

等分别是A1、C1等的单控执行信号。
2)对于有障碍的主令信号,如果能找到一个记忆元件K,使得它的全部障碍段被消除,而执行段被保留,则消障后所得到的新信号,既是双控也是单控执行信号。如图42.6-3中

为K的关断信号是为消除d0与c0之间的障碍。
3)若已知某动作的单控执行信号,则此信号的逻辑“非”就是其相反动作的单控执行信号。如图42.6-3中,已知A0、B0的单控执行信号分别为

则A1的单控执行信号,加入启动信号g是

B1的单控执行信号是
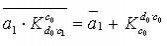
4)对于有障碍的主令信号,若能找到另一个主令信号的“非”信号,作为制约信号,使得消除全部障碍段,而保留执行段和全部自由段,则消障后的信号既是双控也是单控执行信号。图42.6-3中的

既是D1的双控也是单控执行信号。
(3)单控主控阀回路逻辑原理图的绘制
主控阀有两个输出信号,为考虑因事故造成控制气(电)信号断气(电)时,由于主控阀的弹簧作用,使每个气缸均能自动复位的原则,应选择每个气缸两个动作中在程序内先出现的哪一动作的执行信号,作为主控执行信号。按此原则,程序A1B0D1C1D0B1A0C0应选择A1、B0、D1、C1的执行信号作为单控执行信号。图42.6-10为上述程序的单控席子控阀控制回路的逻辑原理图
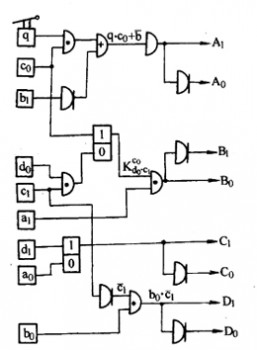
图42.6-10 气控机械手单控主控阀控制回路逻辑原理图
(4)单控主控阀气控回路图的绘制
回路原理图可根据逻辑原理图或直接由X-D图中的单控执行信号画出。图42.6-11是气控机械手的单控主控阀回路原理图,实际应用此回路时,应加入手动操作等部分。
2.1.3中间记忆元件数量的确定及布置方法
前两节内容谈到消除Ⅰ、Ⅱ障碍信号可选用中间记忆元件,本节分析记忆元件数量的确定及其布置方法。
(1)连续一次往复次数的确定
在气缸动作状态程序式中,若相邻字母相同而角标状态相反,则称为连续一次往复。连续一次往复总次数由下式确定

式中 W1——单个气缸连续一次往复运动次数;
W2——两个气缸连续一次往复运动次数;
Wi——i个气缸连续一次往复运动次数;
r——计算气缸数,对单往复系统,r=n-1,对于多往复系统,r=n;
n——程序式中气缸数。

图42.6-11 气控机械手的单控主控阀回路原理图
例3 试计算程序式[A1B0C0A0B1C1D1D0E1E0]的连续一次往复运动的总次数。由程序式可知,为单往复系统,气缸数n=5,计算气缸数r=5-1=4。即最多可以计算到四个缸的连续一次往复,单缸连续一次往?复有D1|D0、E1|E0所以W1=2。因无双缸连续一次往复,所以W2=0,三缸连续一次往复有A1B0C0|A0B1C1,因相邻的三个字母相同而角标状态相反,所以W3=1,因无四缸连续一次往复,则W4=0,连续一次往复总次数为W=W1+W2+W3+W4=2+0+1+0=3
应注意,当连续一次往复的划分方法不止一种时,只能任取一种。否则将使控制回路复杂化。例如在多往复程序式[A1B1A0B0C1B1C0B0]中,有A、B、C三个气缸,n=3,则计算气缸数r=n=3,W1=0、W3=0,双缸往复有两种分法分别记为A1B1|A0B0、C1B1|C0B0或B0A1|B1A0、B0C1|B1C0。上述两种分法结果相同都是W2=2,而不能写为W2=2+2=4。又例如在多往复程序式A1B1B0B1B0B1B0A0中,共有六次连续一次往复,记为B1|B0|B1|B0|B1|B0、A0|A1,因是多往复系统,r=n=2,可取W1=6,W2=0,W=W1=6。
(2)中间记忆元件数量的确定
中间记忆元件数可由下式计算

式中 j——中间记忆元件数;
Zhs——表示只取整数部分,小数部分舍去。如果W=0,一般不需加中间记忆元件。
例4 判别,计算程序式[A1B1B0C1C0A0]、[A1B1C1D1C0D0A0B0]中连续一次往复总次数和所需中间记忆元件。因程序式[A1B1B0C1C0A0]是单往复系统,所以r=n-1=2,只需计算到两个缸。单缸一次往复有B1|B0、C1|C0、A0|A1,因此W1=3,W2=0,W=W1=3。记忆元件数
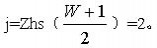
因程序式
[A1B1C1D1C0D0A0B0]是单往复系统,所以r=n-1=4-1=3,则只需计算到三个缸。双缸连续一次往复有C1D1|C0D0、A0B0|A1B1,因此W2=2,W1=0,W3=0,W=W2=2。记忆元件数

(3)在X-D线图中中间记忆元件的布置方法
为使主控信号逻辑表达式简化,中间记忆元件可按下方式布置。
1)按连续一次往复动作分界线布置,中间记忆元件的切换线应尽量选取连续一次往复动作的分界线。因该切换线上有脉冲信号,选用脉冲信号作为记忆元件的通信号t和断信号d,二者不会产生障碍。如程序式[A1B1B0A0]中,为消除主控信号的障碍,可选用一个中间记忆元件即j=1,其布置方式如图42.6-12所示。其中b1、a0分别为记忆元件的通、断信号。
2)按阶梯形式布置>当中间记忆元件的个数j>2时,为使记忆元件的通信号t1、t2、t3……和断信号d1、d2、d3形成的程序式不产生障碍,可采用阶段形式布置,如图42.6-13。
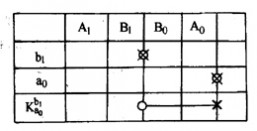
图42.6-12 按连续一次往复动作分界线布置中间记忆元件

图42.6-13 按阶梯形式布置中间记忆元件
a)j=2;b)j=3;c)j=3)
气动系统设计的主要内容及设计程序
气动系统设计的主要内容及设计程序
3.1 明确工作要求
1)运动和操作力的要求 如主机的动作顺序、动作时间、运动速度及其可调范围、运动的平稳性、定位精度、操作力及联锁和自动化程序等。
2)工作环境条件如温度、防尘、防爆、防腐蚀要求及工作场地的空间等情况必须调查清楚。
3)和机、电、液控制相配合的情况,及对气动系统的要求。
3.2 设计气控回路
1)列出气动执行元件的工作程序图。
2)画信号动作状态线图或卡诺图、扩大卡诺图,也可直接写出逻辑函数表达式。
3)画逻辑原理图。
4)画回路原理图。
5)为得到最佳的气控回路,设计时可根据逻辑原理图,做出几种方案进行比较,如对气控制、电-气控制、逻辑元件等控制方案进行合理的选定。
3.3 选择、设计执行元件
其中包括确定气缸或气马达的类型、气缸的安装形式及气缸的具体结构尺寸(如缸径、活塞杆直径、缸壁厚)和行程长度、密封形式、耗气量等。设计中要优先考虑选用标准缸的参数。
3.4 选择控制元件
1)确定控制元件类型,要根据表42.6-13进行比较而定。表42.6-13 几种气控元件选用比较表
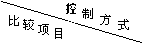
电磁气阀控制气控气阀控制气控逻辑元件控制
安全可靠性较好(交流的易烧线圈)较好较好
恶劣环境适应性(易燃、易爆、潮湿等)较差较好较好
气源净化要求一般一般一般
远距离控制性,速度传递好,快一般,>0几毫秒一般,几毫秒~0几毫秒
控制元件体积一般大较小
元件无功耗气量很小很小小
元件带负载能力高高较高
价格稍贵一般便宜
2)确定控制元件的通径,一般控制阀的通径可按阀的工作压力与最大流量确定。由表42.6-14初步确定阀的通径,但应使所选的阀通径尽量一致,以便于配管。至于逻辑元件的类型选定后,它们的通径也就定了(逻辑元件通径常为ф3mm,个别为ф1mm)。对于减压阀或定值器的选择还必须考虑压力调节范围而确定其不同的规格。
3.5 选择气动辅件
1)分水滤气器其类型主要根据过滤精度要求而定。一般气动回路、截止阀及操纵气缸等要求过滤精度≤50~75μm,操纵气马达等有相对运动的情况取过滤精度≤25μm,气控硬配滑阀、射流元件、精密检测的气控回路要求过滤精度≤10μm。
分水滤气器的通径原则上由流量确定(查表42.6-14),并要和减压阀相同。
2)油雾器根据油雾颗径大小和流量来选取。当与减压阀、分水滤气器串联使用时,三者通径要相一致。表42.6-14 标准控制阀各通径对应的额定流量①
公称通径/mm3Ф6Ф8Ф10Ф15Ф20Ф25Ф32Ф40Ф50
q10-3/m3·s-10.19440.69441.38891.94442.77785.55558.333313.88919.44427.778
q/ m3·h-10.72.5571020305070100
q/L·min-111.6641.6783.34116.67166.68213.36500833.41166.71666.8
① 额定流量是限制流速在15~25m/s范围所测得阀的流量。
3)消声器可根据工作场合选用不同形式的消声器,其通径大小根据通过的流量而定,可查有关手册。
4)储气罐其理论容积可按《气压传动及控制》教材中介绍的经验公式计算,具体结构、尺寸可查《压缩空气站设计手册》。
3.6 确定管道直径、计算压力损失
1)各段管道的直径可根据满足该段流量的要求,同时考虑和前边确定的控制元件通径相一致的原则初步确定。初步确定管径后,要在验算压力损失后选定管径。
2)压力损失的验算 为使执行元件正常工作,气流通过各种元件、辅件到执行元件的总压力损失,必须满足下式

式中

——总压力损失,它包括所有的沿程损失

和所有的局部损失;

[

]——允许压力损失可根据供气情况来定,一般流水线范围约<0.01MPa,车间范围<0.05MPa,工厂范围<0.1MPa。验算时,车间内可近似取[

]≤0.01~0.1MPa实际计算总压力损失,如系统管道不特别长(一般l<100m)。管内的粗糙度不大,在经济流速的条件下,沿程损失

比局部损失

小得多,则沿程损失

可以不单独计入,只须将总压力损失值的安全系数K△p稍予加大就行了。局部损失

中包含的流经弯头、断面突然放大、收缩等的损失

,往往又比气流通过气动元件、辅件的压力损失

小得多。因此对不做严格计算的系统,式(42.6-5)可简化为

式中

——流经元、辅件的总压力损失可通过表42.6-15查出;K△p——压力损失简化修正系数,K△p=1.05~1.3,对于管道较长,管道截面变化较复杂的情况可取大值。如果验算的总压力损失

≤[

],则上边初步选定的管径可定为所需要的管径。如果总压力损失

>[

],必须加大管径或改进管道的布置,以降低总压力损失,直到

<[

]为止,初选的管径即为最后确定的管径。
表42.6-15通过气动元、辅件的压力损失

(MPa)
元件名称公称通径/mm
φ3φ6φ8φ0φ5φ20φ25φ32φ40φ50
额定流量下压力损失≤
方向阀换向阀截止阀0.0250.0220.0150.010.009
滑阀0.0250.0220.0150.010.009
单向型控制阀单向阀、梭阀、双压阀0.0250.0220.020.0150.0120.010.0090.008
快排阀→A0.0220.020.0120.010.0090.008
脉冲阀、延时阀0.025
流量阀节流阀0.0250.0220.020.0150.0120.010.0090.008
单向节流阀P→A0.0250.02
消声节流阀0.020.0120.010.009
压力阀单向压力顺序阀0.0250.0220.020.0150.012
辅件分水滤气器过滤精度
/μm250.0150.025
750.010.02
油雾器0.015
消声器0.0220.020.0120.010.0090.0080.007
注:其它元、辅件可通过实验或按上表各件压力损失类比选定。
3.7 选择空压机
3.7.1 计算空压机的供气量Qj,以选择空压机的额定排气量
Qj可由下式算得
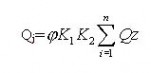
式中 ψ——利用系数;
K1——漏损系数,K1=1.15~1.5;
K2——备用系数,K2=1.3~1.6;
QZ——一台设备在一个周期内的平均用气量(自由空气量)m3/s;
n——用气设备台数。
3.7.2 计算空压机的供气压力pg,以选择空压机的排气压力pg=p+ΣΔp
式中 p——用气设备使用的额定压力(表压)(MPa);
ΣΔp——气动系统的总压力损失。
例10设计某厂鼓风炉钟罩式加料装置气动系统。
加料机构如图42.6-29所示。图42.6-29a中,ZA、ZB分别为鼓风炉上、下部两个料钟(顶料钟、底料钟),WA、WB分别为顶、底料钟的配重,料钟平时均处于关闭状态。图中A与B分别为操纵顶、底两个料钟开、闭的气缸。
图42.6-29 鼓风炉加料装置气动机构示意图
a)剖视图;b)外形示意图解:
(1)工作要求及环境条件
1)工作要求具有自动与手动加料两种方式。自动加料:加料时,吊车把物料运来,顶钟ZA开启卸料于两钟之间;然后延时发信号,使顶钟关闭;底钟打开,卸料到炉内,再延时(卸完料)关闭底钟,循环结束。
顶、底料钟开闭动作必须联锁,可全部关闭但不许同时打开。
2)运动要求料钟开或闭一次的时间t2≤6s,缸行程s均为600mm。所以气缸活塞杆平均速度
要求行程末端平缓些。
3)动力要求顶部料钟的操作力(打开料钟的气缸推力)为FZA≥5.10kN;底部料钟开启作用力为FZB≥24kN。
4)工作环境环境温度30~40℃,灰尘较多。
(2)回路设计
1)列出气动执行元件的工作程序
2)画信号动作状态线图(图42.6-30)
3)画逻辑原理图(图42.6-31)
4)画回路原理图(图42.6-32)
回路图中YA1和YA2为延时换向阀(常断延时通型),由该阀延时经主控阀QFA、QFB放大去控制缸A1和缸B0状态。料钟的关闭靠自重。
(3)选择执行元件
1)确定执行元件类型根据料钟开闭(升降)行程较小,炉体结构限制(料钟中心线上下方不宜安装气缸)及安全性要求(机械支力有故障时,两料钟处于封闭状态),故采用重力封闭方案,如图42.6-9所示。同时,在炉体外部配上使料钟开启(即配重抬起)的传动装置,由于行程小,故采用摆块机构,即相应地采用尾部铰接式气缸做执行元件。
考虑料钟的开启动作是:开启靠气动,关闭靠配重,所以选用单作用缸。又考虑开闭平稳,可采用缓冲型的气缸。因此,初步选择执行元件为两台标准缓冲型、尾部铰接式气缸。
图42.6-30 信号-动作状态线图
图42.6-31 气控逻辑原理图
2)主要参数尺寸 气缸内径D 顶部料钟气缸,其内径由下式计算,即
式中 工作推力F1=FZA=5.1×103N,当υ≤0.2m/s时,η=0.8,p=0.4MPa则
查有关手册,取标准缸径DA=160mm,行程s=600mm。
底钟气缸,由于炉体总体布置限制,气缸的操作力为拉力,由下式计算,即
考虑缸径较大,取上式前边的系数为1.03,且当υ≤0.2m/s时η=0.8,F2=2.4×104N,p=4×105Pa则
查手册,也选择冶金用气缸,取标准缸径DB=320mm,行程s=600mm。
综上,取顶钟气缸A为:气缸JB160×600;取底钟气缸B为:气缸JB320×600,活塞杆直径d=90mm。
3)耗气量计算
缸A:已知缸径DA=160mm,行程s=600mm,全行程需时间t1=6s压缩空气量
缸B:已知DB=320mm、s=600mm、t2=6s,由于缸B的供气端是有杆腔,所以缸B一个行程的耗气量为
(4)选择控制元件
1)选择类型 根据系统对控制元件工作压力及流量的要求,按照气动回路原理图初选各控制阀如下:
主控换向阀:QFA、QFB均为JQ23-L型,通径待定;
行程阀:x0初选为可通过式,其型号为Q23JC4A-L3;
行程阀:a0、a1、b0初选为杠杆滚轮式,其型号为Q23JC3A-L3;
逻辑阀:QF1,初选为JQ230631型两位三通双气控阀;
梭阀:QF2初选为QS-L3型;
手动阀:S初选为推拉式,其型号为Q23R5-L3;
手动阀:g初选为按钮式,其型号为Q23R1A-L3。
2)选择主控阀 对A缸主控换向阀QFA的选择:
因A缸要求压力pB=0.4MPa,流量QA=2.09×10-3m3/s,查表42.6-14初选QFA的通径为φ15mm,其额定流量QA=2.778×10-3m3/s。故初选其型号为Q25Q2C-L15(堵死两个不用的气口)。
对B缸主控换向阀QFB的选择:
因B缸要求压力pB≤0.4MPa流量QB=8.3333×10-3m3/s,故初选其型号为Q25Q2C-L25(堵死两个不用的气口)。
3)选择减压阀 根据系统所要求的压力、流量,同时考虑A、B缸因联锁关系不会同时工作的特点,即按其中流量、压力消耗最大的一个缸(B缸)选择减压阀。由供气压力为0~0.7MPa,额定流量为8.3333×10-3m3/s,选择减压阀订货号为395、291~294。
(5)选择气动辅件
辅件的选择要与减压阀相适应。
分水滤气器:394、49
油雾器:396、49
消声器:配于两主控阀排气口、气缸排气口处,起消声、滤尘作用。对于A缸及主控阀选FXS2-L15,对于B缸及主控阀选FXS2-L25
(6)确定管道直径、验算压力损失
1)确定管径 本例按各管径与气动元件通径相一致的原则,初定各段管径(图42.6-33)。同时考虑A、B缸不同时工作的特点,按其中用气量最大的B缸主控阀的通径初步确定oe段的管径也是25mm。而总气源管yo段的管径,考虑为两台炉子同时供气、由流量为供给两台炉子流量之和的关系
可导出:
取标准管径为40mm。
2)验算压力损失 如图42.6-33所示,本例中验算供气管y处到A缸进气口x处的损失(因A缸的管路较细,损失要比B缸管路的大)是否在允许范围内ΣΔp≤[△p]
图42.6-33 管道的布置示意图
沿程压力损失
① y—o段的沿程压力损失
由式(1-40)
式中 △pl——沿程压力损失;
d——管内径,d=0.04m;
l——管长,l=0.6m;
υ——管中流速,
λ——沿程阻力系数,由雷诺数Re和管壁相对粗糙度 确定。
根据温度30℃,由表42.1-5查得运动粘度υ=1.66×10-5m2/s
根据Re、 查有关手册得λ=0.0265,温度30℃、压力0.4MPa时γ值可由式(42.1-2、42.6-4)算出
② o-e段的沿程压力损失
由 和Re1=2.27×104可查得λ1=0.029
③ e-x段沿程压力损失
可查得λ3=0.035
④ 由y-x的所有沿程损失
局部压力损失
① 流经管路中的局部压力损失
Σζ=ζy+ζ0+ζa+ζe+ζ?+ζg+ζh+ζi+ζj+ζl+ζk+ζx
各局部阻力系数
ζy——入口局部阻力系数ζy=0.5;
ζ0、ζe——分别为三通管局部阻力系数ζ0=2,ζe=1.2;
ζa、ζ?——流经截止阀处局部阻力系数,ζa=ζ?=3.1;
ζh、ζi、ζj、ζk——弯头局部阻力系数;分别为ζh=ζi=ζj=0.29,ζk=2×2×0.29=0.58;
ζl——软管处局部阻力系数,近似计算
ζl=2×
=0.16;
ζx——出口局部阻力系数,ζx=1
② 流经元、辅件的压力损失 流经减压阀的压力损失较小可忽略不计,其余损失:
式中 △pb——流经分水滤气器的压力损失;
△pd——流经油雾器的压力损失;
△pg——流经截止式换向阀的压力损失。
查表42.6-15得△pb=0.02MPa,△pd=0.015MPa,△pg=0.015MPa。
③ 总局部压力损失
总压力损失
考虑排气口消声器等未计入的压力损失:
则
从

的计算可知,压力损失主要在气动元、辅件上,所以在不要求精确计算的场合,可不细算,只要在安全系数K△p中取较大值就可以了。 执行元件需工作压力p=0.4MPa,压力损失
供气压力为
说明供气压力满足了执行元件需要的工作压力,故以上选择的通径和管径是可以的。
(7)空压机的选择
在选择空压机之前,必须算出自由空气量(一个标准大气压状态下的流量)Q′
气缸的理论用气量由下式计算
其中 QZ——一台用气设备上的气缸总用气量;
n——用气设备台数,本例中考虑左右两台炉子有两组同样的气缸,故n=2;
m——一台设备上的用气执行元件个数,本例中一台炉子上有A和B两个缸用气,故m=2;
α——气缸在一个周期内单程作用次数,本例中,每个气缸一个周期内单程作用一次α=1;
Qz——一台设备中某一气缸在一个周期内的平均用气量,本例中Q′A=9.95×10-3×10-3m3/s,Q′B=3.68×10-2m3/s;
t——某个气缸一个单行程的时间,本例中tA=tB=6s;
T——某设备的一次工作循环时间,本例中T=2tA+2tB=24s。
若考虑左右两台炉子的气缸都由一台空压机供气,则气缸的理论用气量
取设备利用系数φ=0.95;漏损系数K1=1.2;备用系数K2=1.4。则两台炉子气缸的理论用气量;
如无气源系统而需单独供气时,可按供气压力≥0.5MPa,流量Qj=2.08m3/min,查有关手册选用4S-2.4/7型空压机,该空压机的额定排气压力为0.7MPa,额定排气量为2.4 m3/min(自由空气量)。
四 : 36电脑全自动手套机控制系统设计
第",卷第/期?测试与控制?#!!$年,月
机电产品开发与创新
7898:;<=8>?@->>;9A?B;>;CDAEFB>8GH@I:8E?GBEA:0G;JKE?L
()*+",-.)+/
012+-#!!$
电脑全自动手套机控制系统设计
朱
昊,汪木兰,左键民,胡艳艳
$"&&"()
(南京工程学院先进数控技术江苏省高校重点建设实验室,江苏南京
摘要:介绍了电脑型全自动手套机的工作原理。以!"#$%单片机为核心,结合液晶显示电路、开关量输
入输出电路、键盘矩阵电路、&’()!*通信电路等,构建了控制器的硬件系统。讨论了软件系统实现的功能,分析了控制原理,并给出了软件程序框图。实际应用表明,本系统的设计方案合理可行,稳定可靠,具有较高的性价比和实用价值。
关键词:手套机;单片机;数控系统中图分类号:30$);34"
文献标识码:5
文章编号:"&&$6++)(($&&+)&*6"(&6&(
!引言
随着人们劳动安全意识的提高和追求时尚的需求,
了电子系统与机械系统相结合的方式,以用户键盘输入的指令及参数和各种机械微动开关的动作为输入,经程序处理后,一方面通过变频器控制电动机提供主动力,另一方面通过电磁铁的动作来控制手套机的机械系统。此外系统还配置了液晶显示屏,液晶显示屏上可以实时地反映手套的编织进度,以及当前时刻的各项参数。
图5
全自动手套机外形图
手套已成为日常生活中不可缺少的日用品。手套编织机也由手动控制型过渡到了电脑全自动控制型,同时手套机的数量和功能都在不断增加。编织的手套品种一般包括了劳保手套、各种魔术型时装手套、五趾袜系列、半指手套、全指手套、防寒手套以及时尚流行手套等,规格具有大、中、小号各种尺寸。由于电脑全自动手套机既可以用于家庭生产,也可以组织大规模形式的企业生产,所以国内的需求量比较大。目前,包括电脑手套机在内的自动针织机械的核心控制系统生产商主要集中在欧洲、日本和台湾,国内的手套机生产厂商大多数引进国外的控制器
!"#
在手套编织的过程中,"#$%5
"#$6(+.,,6//’61.-’1#0
$/.7+82#11#2$-’09#2+
。因此,自行研制具有自主知识产权的
手套机核心控制系统一方面可以大大减少手套机的生产成本,另一方面也可以方便产品的使用和维护。
#电气控制系统硬件设计
!$#
"手套机电气控制系统工作原理
电脑型全自动手套机是一个典型的机电一体化控制
考虑到控制器的开发成本和技术的成熟性等问题,本系统以%&’($单片机为核心,用$)’*"$作为程序存储器,用+$+,作为数据存储器。由于系统开关量输入输出及键盘输入需要占用大量输入输出接口,系统配置一片%$**用于扩展-./端口。控制系统的硬件结构框图如图$所示。
左右基准脉冲信号’01和’02由传动链上的挡光板输入。手套机工
图!
电气控制系统硬件结构图
左右基准脉冲输入
体系。它由机头、机身、控制器、针筒、控制鼓、剪刀及辅助机构等部分组成,其外形如图"所示。手套机的自动编织工作主要依靠电气控制系统控制针筒、控制鼓及电磁铁来实现。控制系统以机头的左右移动为基准,通过接收各种输入信号,同时控制多个电磁铁协调运动来完成手套的编织过程。
根据对手套编织机的功能和需求分析,本系统采用
收稿日期:#!!$%!&%"’
基金项目:江苏高校高新技术产业发展项目(+,-"*(%!)作者简介:朱昊(./!"(),男,江苏南京人,助教,硕士。主要研究方向:数控技术、信号检测与处理。
1’7($,&M"$%N
’01
’02
",路电磁铁开关量输出246,%*变频器
%&’($
)路微动开关输入
$)’*"$
"+键键盘输入
%$**
+$+,
电动机
"#$%!&’()*’(+,(’-+.,+/+01(.2#0’/0.21(./3431+-
作时,机头沿导轨作往复运动,机头往复运动一个周期,手套机的机械系统编织完两行。当机头运行到导轨左右两端时,挡光板分别输出!"#和!"$信号。!"%系统根据这个基准信号的时序来控制开关量输出信号的时序。
微动开关输入信号是除!"#和!"$信号以外的另一组开关量输入信号。包括断纱检测、手柄状态、离合器位置、手套落下脉冲、支点移动、针筒和控制鼓等&个输入信号。它们的变化反映了手套编织过程中各个阶段的转换以及是否有异常情况发生。
电磁铁开关量输出包括刹车、剪刀控制、吹气、凸轮切换等’(路信号。这’(路开关量输出信号以!"#和
频器输出之间均串接了光电耦合器,用于隔离电气干扰,经实际使用表明效果较好。
!电气控制系统软件设计
实际编织通过电磁铁的吸合,依靠控制鼓和针筒的
相互作用实现手套的自动编织。系统上电后,按照“小指尖!小指筒!无名指尖!无名指筒!中指尖!中指筒!食指尖!食指筒!四指掌过渡!四指筒!大拇指尖!大拇指筒!五指掌过渡!五指筒!手腕B套口加橡筋线C!热熔纱!空走”这个’&个步骤顺序进行编织。每个步骤都有各自的电磁铁输出时序,各时序均以!"#和!"$信号为基准,根据手指或手掌的粗细、长短的不同,在适当的时刻控制’(个电磁铁动作,进而使手套机的各机械部分相互配合工作,以实现手套的自动编织。在开始编织之前用户可以更改参数,包括手套各部分的长度、橡筋线的条数、编织速度、一次性编织手套的个数等。编织过程中,用户可以选择暂停或中止编织。
在手套的编织过程中,液晶显示屏可以动态显示手套的编织过程。显示屏左边为手套的轮廓图。手套编织时,该图形可以相应地描绘当前手套的编织状态。随着编织的进行,手套图形实时更新。屏幕右边为菜单和文字显示区,在编织过程中显示手套编织过程中的实时数据以及当前可执行的操作。
电气控制系统软件由主程序和两个外部中断服务程序组成
@3A
系统上电初始化
!"$的时序为基础,根据各自的时序输出,控制相应电
磁铁动作,使得系统的各机械部件相互配合,以自动完成手套的编织过程。
’)键键盘采用(*(矩阵输入方式,系统利用外部中
断方式检测键盘输入信号。
系统的显示模块选用+,#-.(/’.01模块。它由控制器1)2)3!、列驱动器1)432、行驱动器1)4(/以及与外部设备的接口等几部分组成,既能显示字符,又能显示图形,分辨率为.(/*’.0。显示系统与!"%的接口电路如图3所示。该模块的数据总线与0/!3.的数据口直接相连。0/!3.的$567$作为液晶显示模块的读写控制信号。液晶显示模块的$8-81接$!复位电路。!8
信号可由地
’/
40
4’?$57$D?<
’&0&)?23
+,#-.(/’.015/5&!65!8$57$$8-8
<EE
’2./
址线译码产生。!65信号由0/!3.地址线40提
"’;)
。如
系统复位(端口、存储器、通信和菜单等)
图(所示程序,主程序用于实现系统状态检测、编织参数设置、按时序控制电磁铁输出、根据输入参数,通过变频器控制电动机转速和显示屏的动态模拟等功能。两个中断服务程序分别为键盘中断服务程序和微动开关中断服务程序。键盘中断程序实现在编织过程中对系统的相关操作以及参数的改变。微动开关的作用是:当有不正常情况发生时,系统可以诊断故障的种类,并在显示屏上显示当前的状态以及用户可以进行的操作。
否否否
:-,>5
</
’0
供:409’为指令口地址;
显示手套图形及公司商标
:,
是否有设置键按下?
是
运行参数设置子程序
(
409/为数据
口地址。:-为字体选择控制,接至
’
.
是否有确认键按下?
是
显示准备界面
否
0/!3.的"’;)
脚用于字体
选择。</为负电源输入。
由于单片机自带的$-=.3.!串行通信接口有传输距离较短、抗干扰能力不太强等缺点,所以本系统通过
系统是否已在零位?
是
是否有启动键按下?
是
显示自动编织运行界面
->&?’&)芯片将0/!3.上的$-=.3.!通信转换成$-=(0?通信,用于控制变频器的输出频率。
本系统中含有大量电磁铁,电磁铁在动作时,触点的吸合与松开会通过多种途径对控制电路的直流电源以及信号传输造成瞬时干扰
@(A
按时序运行’&个编织步骤,动态更新界面,直至编织完成
。因此,整个微机系统与基
准脉冲输入、微动开关输入、电磁铁开关量输出以及变
(下转第!"#页)
"结束语
采用6$%可编程控制器对小接地电流系统单相接地
除故障提供了强有力的技术支持。参考文献:
(!)张桂香*电气控制与6$%应用(+)*化学工业出版社,#000*航空航天大学(#)王永华*现代电气控制及6$%应用技术(+)*北京:
出版社,#00!*
进行显示,接线非常简单,只要把每一条进出线的接地信号送入6$%,就可以得到准确的接地线路编号的显示。原来许多复杂的设备接线都可以利用6$%软件(程序)取代,必将提高预告信号的精确度,为供电人员排
(’)刘介才*供电工程师技术手册(+)*机械工业出版社-!..7*
>:"-$&%,"?@:4#"A4+*:9’&$*’+’(-/4,,A4+*:?52++"&*
-321,*41,-3&41,51.6,"7-1.6
-.#*"/B4#"=’&CD)
JR’$#$F)/#77’.%"4#7S.-0)&&"-$#79)4:$-7-%*8-77#%),T:’U:-’R’$#$P>=???,8:"$#L
3;#*+45*:V:)$/:)&6#77)#./:H4’..)$/&*&/)6,.)#B&2-D$&"$%7)HA:#&))#./:,’&)&S+8/-,)A-&&",7)/-2)6-$&/.#/)#44’.#/)7*/:)0#’7/*7"$)C</"#$/#%)-’&4#..")&-$/:)A.-6A/&).3"4)"$/:)/)4:$"4#7A).&-$$)7C9:"&#./"47)D"776#B)/:)&"6A7)"$/.-2’4/"-$/-/:"&6)/:-2C8".<’+=#:G6#77)#./:H4’..)$/&*&/)6;&"$%7)HA:#&))#./:;4-$/.-7-0
S+8
(上接第>@>页)
!结论
本文提出的电脑型全自动手套机电气控制系统实现
(’)手套机中电磁铁数量很多,电磁铁动作会通过串行或辐射的方式对控制电路造成干扰。因此对于电磁铁电路部分需要增加光电耦合器、灭弧器、滤波器等。本系统现已正式投入使用,经实践证明,该系统工作稳定、可靠性强,且具有较高的性价比和良好的实用性。参考文献:
(!)邓秀琴*羊毛衫加工原理与实践(+)*北京,中国纺织出版社-!..!*(#)黄元顺*新型电脑横机主要控制机构结构设计分析(/)*中国纺织
大学学报-#000-!0*
张彦斌*+%123!系列单片微型计算机及其应用(+)*西(’)薛钧义,
安交通大学出版社-!..4-#*
陈霞*数控机床的抗干扰措施(/)*机械制造-#005-’*(")王申银,
的难点主要体现在如下几个方面:
(!)需要理清!"个电磁铁之间相互配合的时序关系。各电磁铁之间运行逻辑的严密性和时间准确性都有很高的要求,任意一个电磁铁的任意一次时序配合都不能发生错误,否则都可能导致产品编织失败。
(#)动态图像模拟要求$%&的图像部分可以实时反映手套编织的过程;字符部分可以实时刷新各项参数,并且应当显示当前系统的工作状态和用户可进行的操作。
!"#$%&’()’&*+’,-.#*"/0#$&%(’+32*’/4*$56,’7"8&$**$&%945:$&"
!"#"$%,&’()*+,-$.,!#/01$.,*1.,"#2$.,2$.
(!"#$%&’()*+#,-.#/-.*-0123#$4)25’6)."4#78-$/.-79)4:$-7-%*,5#$;"$%<$&/"/’/)-09)4:$-7-%*,5#$;"$%!"#$%&’=>??>@,8:"$#)
3;#*+45*:9:"&A#A)."$/.-2’4)&/:)A."$4"A7)-00’77#’/-6#/"4%7-3)B$"//"$%6#4:"$)C9:):#.2D#.)&*&/)6"&2)&"%$)2ED:"4:’&)&
/:)<$/)7F8GHI>&).")&&"$%7)4:"A6"4.-A.-4)&&-.JK?8@=LE+8M4".4’"/E&D"/4:&"%$#7"$A’/N-’/A’/4".4’"/EB)*,-#.2#..#*4".4’"/#$2OGHPKI4-66’$"4#/"-$4".4’"/E)/4C9:)&-0/D#.)0’$4/"-$#$24-$/.-7/:)-.*#.)2"&4’&&)2"$2)/#"7CQ"$#77*E/:)4-..)&A-$2"$%6#"$A.-%.#607-D4:#./"&A.)&)$/)2C9:)#AA7"4#/"-$2)6-$&/.#/)&/:#//:)A.-A-&)2&/.#/)%*"#"7#,7)E.)#&-$#,7)E&/#,7)#$2.)7"#,7)C9:"&&*&/)6:#&:"%:A).0-.6#$4)#$27-D4-&/C
8".<’+=#:%7-3)B$"//"$%6#4:"$);&"$%7)4:"A6"4.-A.-4)&&-.;4-6A’/).$’6)."4#74-$/.-7&*&/)6
本文标题:
电气传动控制系统设计-17SDYSC-1山地运输车传动系统的设计 本文地址:
http://www.61k.com/1061082.html